Enabling chipmakers to power the future
Navigating Semiconductor Manufacturing Pressures
Semiconductor manufacturers face relentless pressure from market volatility, increasing production complexity, and a critical talent shortage. Thriving in this environment demands exceptional operational agility and efficiency.
The High Cost of Fragmented Decisions
The fab’s success depends on countless complex, interconnected decisions, aiming to translate high-level business goals – like increasing throughput, reducing cycle times, or prioritising urgent orders – into effective factory floor operations. Yet, many fabs rely on legacy systems and siloed teams, making suboptimal decisions based on past data without foresight capabilities. This fragmented decision-making erodes efficiency, and loss in capacity can translate into hundreds of millions of dollars in lost revenue annually.
The Shift to Autonomous Operations
Faced with these pressures, the dominant trend in the industry is moving towards greater automation and autonomy in operation. This requires an “intelligence layer” – a factory brain – to make smart, predictive decisions and orchestrate operation for optimal performance and adaptability.
Flexciton: Your Partner for Autonomous Decisions
Flexciton delivers this critical intelligence layer. We replace legacy planning and scheduling with autonomous, intelligent decision-making powered by mathematical optimisation and AI. Flexciton determines the optimal what and when for factory floor operations, providing the smart decisions needed to guide execution systems and enable revenue-to-shop-floor alignment. As the Autonomous Technology partner, Flexciton orchestrates your manufacturing operations, dramatically improving your factory agility and performance, powering your transition to an Autonomous Fab.
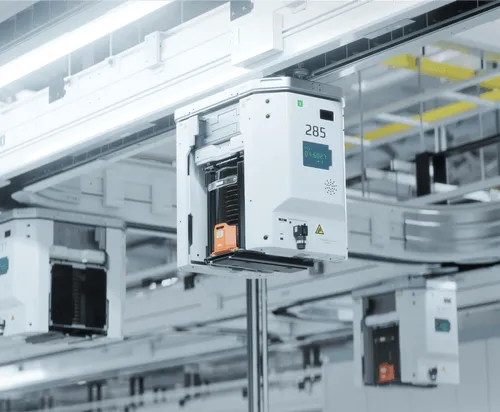
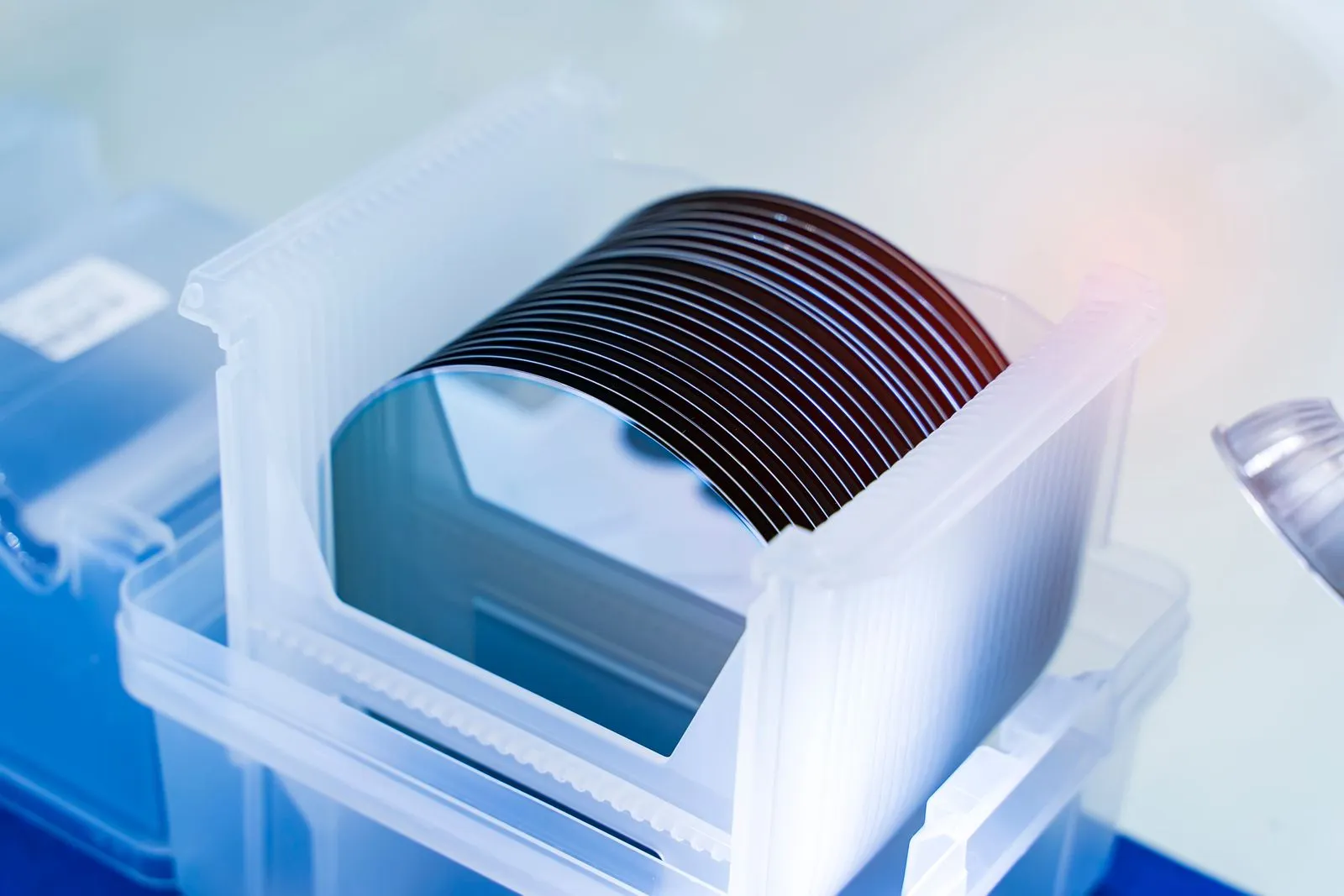
Meet the
leadership
Flexciton’s co-founders spent years in the industry, seeing first hand the problems that manufacturers face when planning and scheduling production. Companies recorded vast amounts of data about their operations, but they struggled to learn anything meaningful from it.
Through their combined technical experience in optimization, data science and computer programming, Jamie and Dennis started to uncover how insights could be learnt from this industrial data to drive significant efficiency improvements.
Serving as CEO, Jamie drives the company's vision of enabling autonomous factories. He led the commercialisation of Flexciton's cutting-edge technology within the industry and expanded its global customer base across the US, Europe, and Asia. Under his leadership, the product suite grew to a comprehensive Autonomous Technology offering and the company secured over £22.5 million in private and government funding.
Jamie is a founding member of the SEMI Smart Manufacturing Committee for Europe and has represented the UK deep tech sector in the UK government. An Oxford graduate (top of his year in Mathematics & Statistics), he was named to the Forbes 30 Under 30 list in 2018.
As CTO, Dennis Xenos turns bold ideas into factory-floor results. With a PhD in industrial optimisation from Imperial College London, he co-founded Flexciton, built its models-first platform, and recruited a world-class team.
His hybrid optimisation technology is present in some of the world’s most complex factories, unlocking hidden capacity worth tens of millions per site.
Under his leadership, Flexciton has secured multi-year contracts across Europe, the US, and Asia, and published research shaping smart manufacturing. He’s an active member of the SEMI Smart Manufacturing America and a frequent speaker on autonomous production.
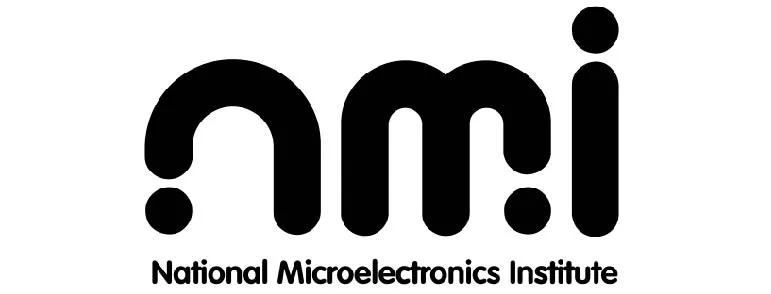
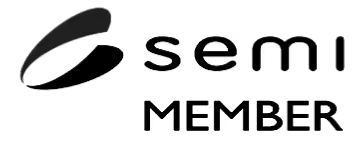
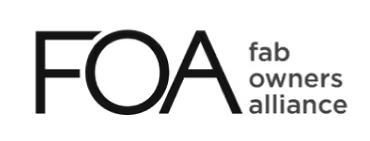
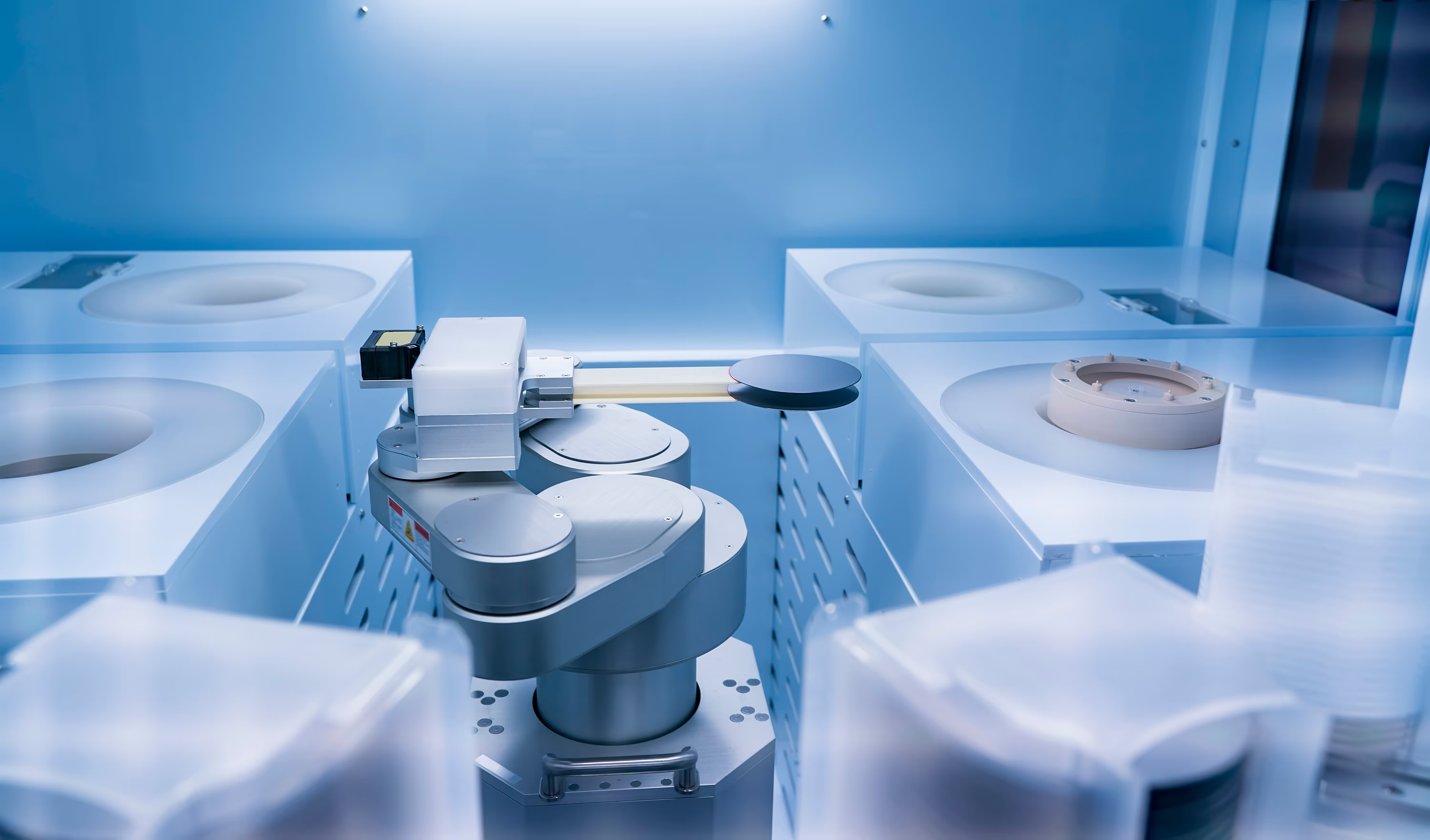
Be part of a revolution. Join us.
We are people from all walks of life with one unified belief: that our product can change manufacturing forever.
Useful resources
Stay up to date with our latest publications.