Five Reasons Why Your Wafer Fab Should Be Using Hybrid Optimization Scheduling
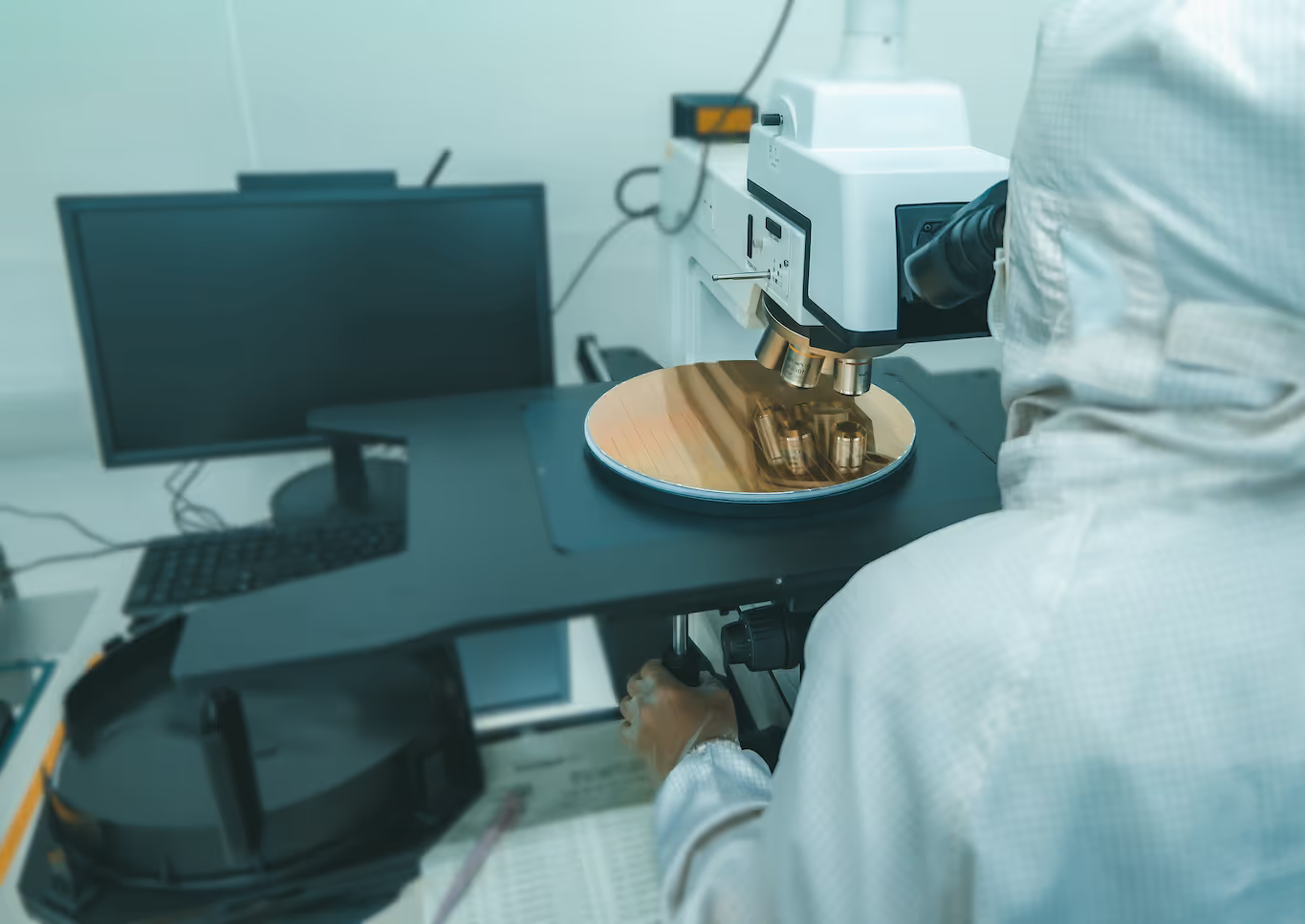
In order to maintain high margins, the cost of manufacturing semiconductors needs to continually diminish. Previously, this had been achieved by increasing the wafer size and shrinking the size of the chips whilst increasing the density of transistors. However, as the effects of these tactics begin to culminate, the future of maximising a wafer fab’s capacity lies within optimizing operational processes.
The process of manufacturing a semiconductor chip is exceedingly complex, often requiring thousands of unique steps. Reducing cycle times and increasing throughput in such an intricate production process calls for very high production efficiency. Fabs usually approach this in one of two ways; the heuristic approach, which is fast but not optimal and the mathematical approach, which is optimal but time-consuming. In order to attain optimal results that are able to keep up with changes on the factory floor, however, fabs need to switch to advanced production scheduling.
The hybrid approach
At Flexciton, we are pioneering a new model that combines the two different methods with a hybrid technique. With this ground-breaking new model, which we call advanced mathematical hybrid optimization technology, optimal results are delivered in a matter of minutes.
Here are 5 reasons your fab will benefit from switching to an advanced scheduling solution:
It's quick
The most complex of scheduling problems can be solved in less than 5 minutes, delivering near-optimal results. This makes the hybrid technique perfect for the dynamic fab environment, since updates can keep up to speed with changes on the factory floor.
Accommodates all constraints
Hybrid optimization is able to realise fully accurate schedules by accommodating all constraints. This ensures a true representation of all activity in the fab, as well as its limitations.
Optimal schedules
By employing mixed-integer linear programming (MILP), Flexciton’s hybrid method guarantees high-quality solutions. Thanks to performance enhancing decomposition, final solutions are very near to the global-optimal.
Low maintenance
With MILP being the core of the solution, high performance can more easily be maintained with very little upkeep. With changes in objectives and recipes constantly taking place, not every consecutive shift in a fab is alike. Despite this, Flexciton’s solution can take into account all aims and constraints and consistently calculate an optimized schedule.
It's adaptable and easy to alter
When needed, constraints and parameters can be altered without the need to rewrite or redesign extensive amounts of new code. Not only this, but hybrid-optimization scheduling can also be rolled out into the entirety of a fab (global scheduling) as well as multiple fabs, even when they have differing production characteristics.
Hybrid optimization could be the answer to your fab’s scheduling problems. Download our white paper to find out more.
Useful resources
Stay up to date with our latest publications.
Speak to one of our experts
Book a demo session or simply reach out to one of our experts to learn more about what Autonomous Technology could do for your fab.
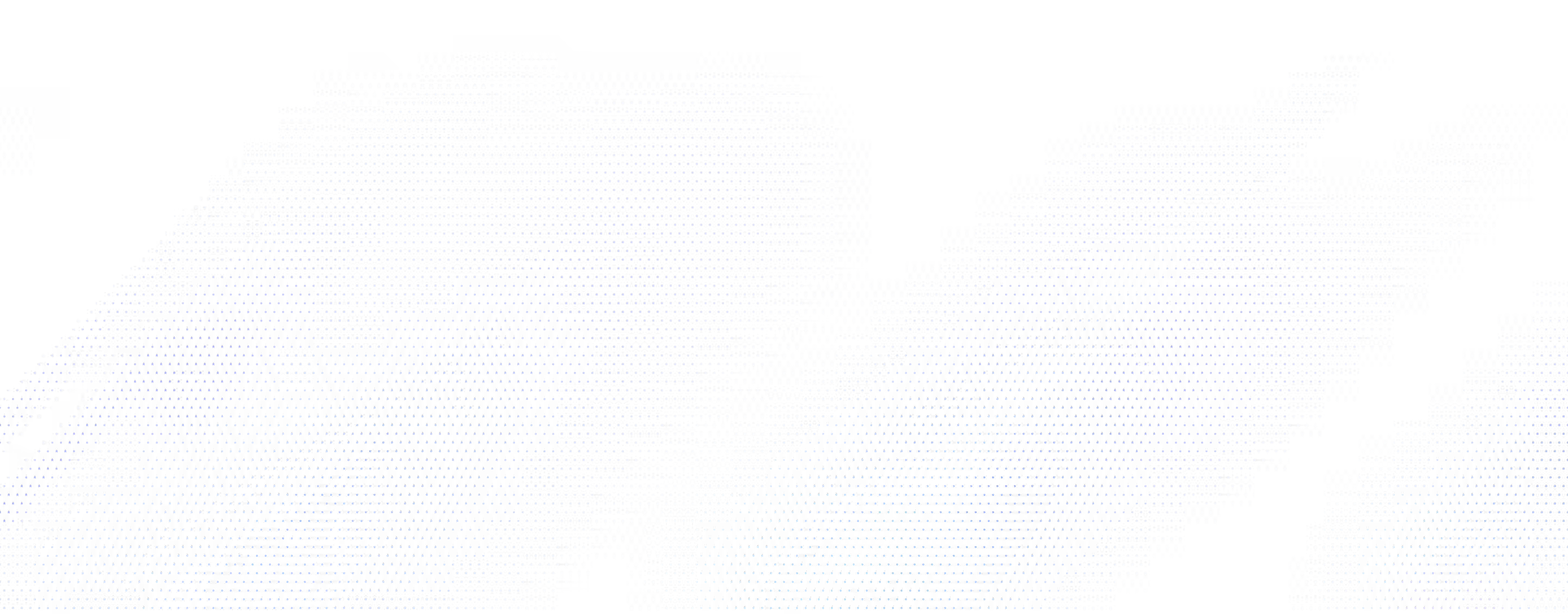