A is for AI
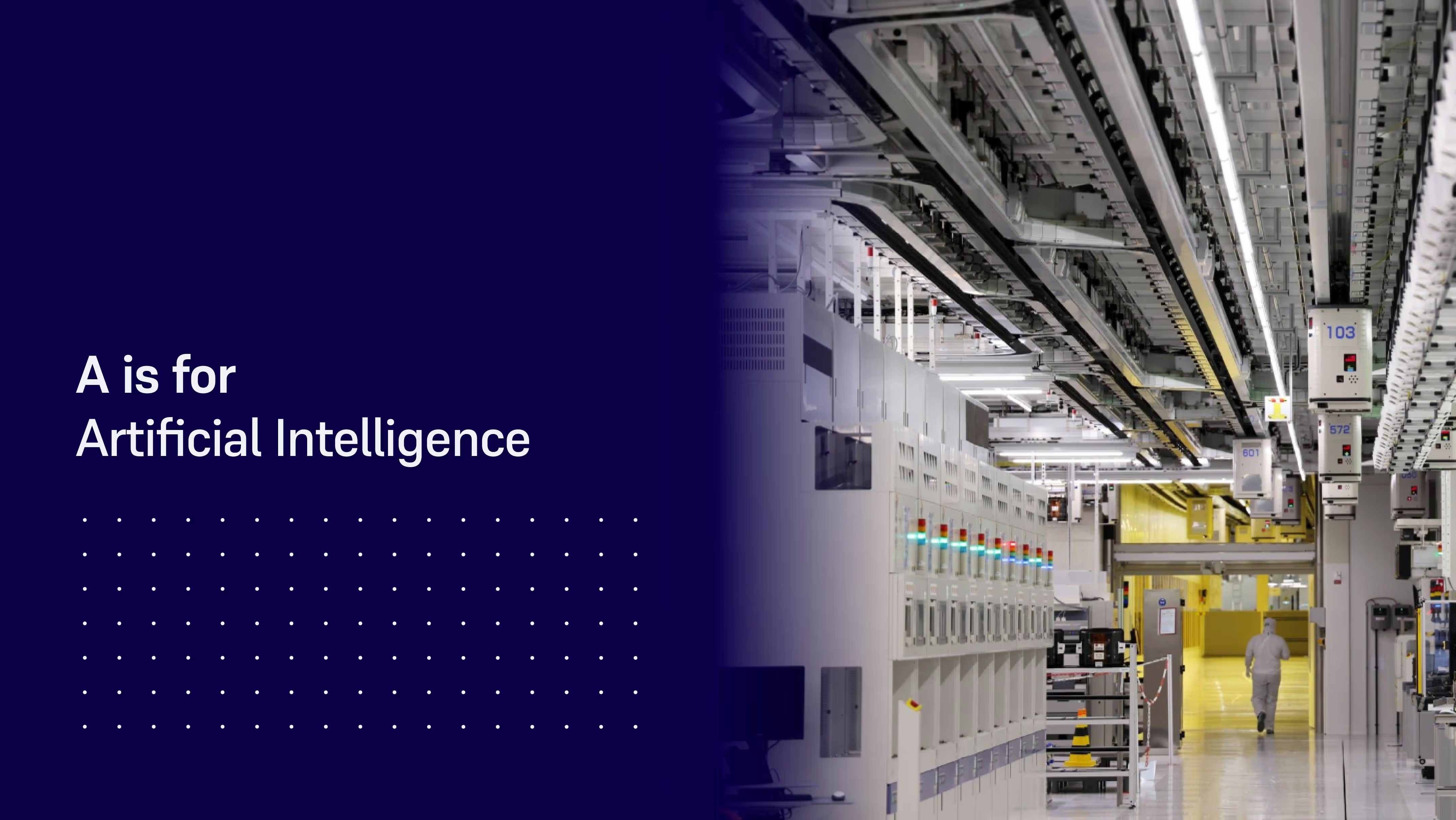
We are excited to introduce the Flexciton Tech Glossary Blog Series: A Deep Dive into Semiconductor Technology and Innovation.
In an ever-evolving semiconductor industry, understanding the nuances of new technologies and the transformative potential of artificial intelligence and optimization is paramount. The Flexciton Tech Glossary Blog Series is designed to shed light on specific technologies and innovations, offering insights into how these advancements can revolutionise semiconductor manufacturing operations.
Each article in this series will delve into a distinct theme, aiming to equip any practitioner in the industry from industrial engineers and manufacturing experts up to VP level professionals with the knowledge to integrate these innovations into their daily operations.
Beyond our in-house expertise, we’re excited to collaborate with industry experts, inviting them to contribute and enrich our series with their specialised knowledge and experience. Join us on this enlightening journey as we explore the frontiers of the semiconductor industry from A-Z.
AI will transform the semiconductor industry
Artificial Intelligence (AI) has become a transformative force in various sectors, driving a global wave of innovation and automation. Seemingly overnight, systems like ChatGPT that harness the primary human interface – natural language – have revolutionised how we interact with technology. In a similar vein, generative art technologies have reinvented our relationship with creativity, making it more accessible than ever before. These remarkable systems have acquired their capabilities through learning, fueled by training on vast amounts of data. This ongoing revolution prompts the question: what is the next frontier to be conquered?
Beyond the novel consumer applications leading the charge, the implications of AI in specialised fields, such as semiconductor manufacturing, are equally profound. Estimates place the earnings already achieved by AI across the semiconductor value chain at over $5 billion. The range of applications is immense and spans activities at all levels. From informing capital allocation, to demand forecasting, fab layout planning, and right down to chip design, AI can enable automation and increase efficiency. Semiconductor manufacturing, in particular, has been identified as the function presenting the most attractive opportunities, where the potential savings have been calculated to be over $10 billion in just the next few years [1].
Impact at all levels
The semiconductor industry is facing several challenges where AI can make a significant impact. These span all the industry’s key activities: long-term capacity planning, research & design, sales, procurement and, of course, manufacturing. Some use cases that are increasingly gaining traction are:
- Supply Chain Optimization: Predictive analytics can forecast demand, optimize inventory levels, and enhance the overall efficiency of the supply chain [2].
- Automated Material Handling Systems (AMHS): Utilising AI-driven cognitive robotics within AMHS automates material transportation throughout the plant [3], optimizing production planning considering AMHS [4].
- Predictive Maintenance: AI can predict when equipment is likely to fail or require maintenance, reducing downtime and increasing overall equipment efficiency [5].
- Defect Detection: Advanced image recognition algorithms can identify defects in wafers at an early stage, ensuring higher yields and reducing wastage [6].
- Virtual metrology: AI can be deployed to estimate a product’s quality directly from production process data. This enables real-time quality monitoring without additional measuring steps [7].
- Process control: AI can analyse vast amounts of data to optimize the manufacturing process, ensuring the best conditions for each step and improving the overall quality of the chips (e.g. tool matching) [8].
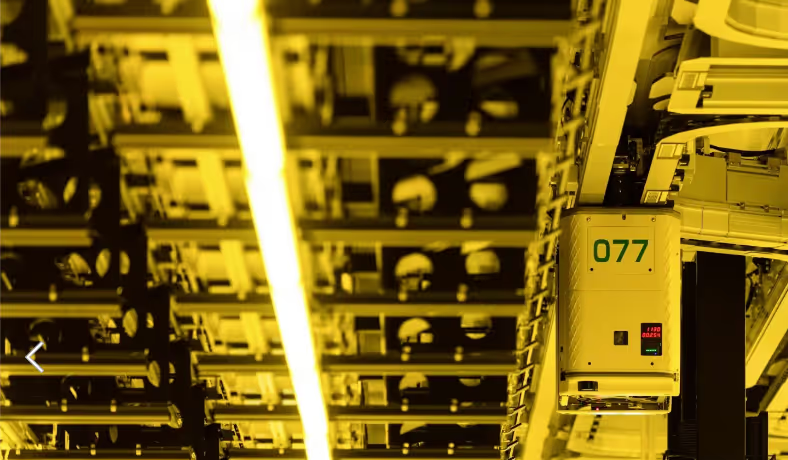
In this article, we focus on AI’s potential to automate scheduling within a semiconductor wafer fab and improve key metrics: increase the throughput of manufacturing lines, reduce cycle times and improve on-time delivery. But first, we step back and define both intelligence and artificial intelligence.
Defining intelligence
Defining intelligence has been a long-standing challenge, with various perspectives offered. A widely-accepted definition, which broadly aligns with the context of semiconductor applications, is as follows:
Intelligence is the ability to accomplish complex goals.
As suggested by Max Tegmark [9], intelligence is not universal but depends on the defined goal. As such, there are many possible types of intelligence. Extending this concept further, intelligence can be characterised according to the following features.
Goal type: Intelligence can be technical (problem-solving), social (interaction), or creative (idea generation).
Skill level: This is typically categorised as below/equivalent/super-human level. This determines whether we aim to match the performance of a human or surpass it.
Scope: Narrow intelligence specialises in a specific task, while broad intelligence encompasses a wide range of tasks like human intelligence.
Autonomy: Intelligence can operate with varying degrees of independence, from human-guided to fully autonomous.
In semiconductor scheduling, super-human performance level is necessary to sift through billions or even trillions of candidate solutions to derive optimal decisions, whilst adhering to complex constraints. Focusing on the narrow scope of scheduling allows the system to specialise, thereby optimizing its performance for these specific requirements. The technical nature of the task calls for a solution that exploits the strictly technical aspects to achieve superhuman performance. Finally, a system with high autonomy and no need for human intervention is desired in such a dynamic environment.
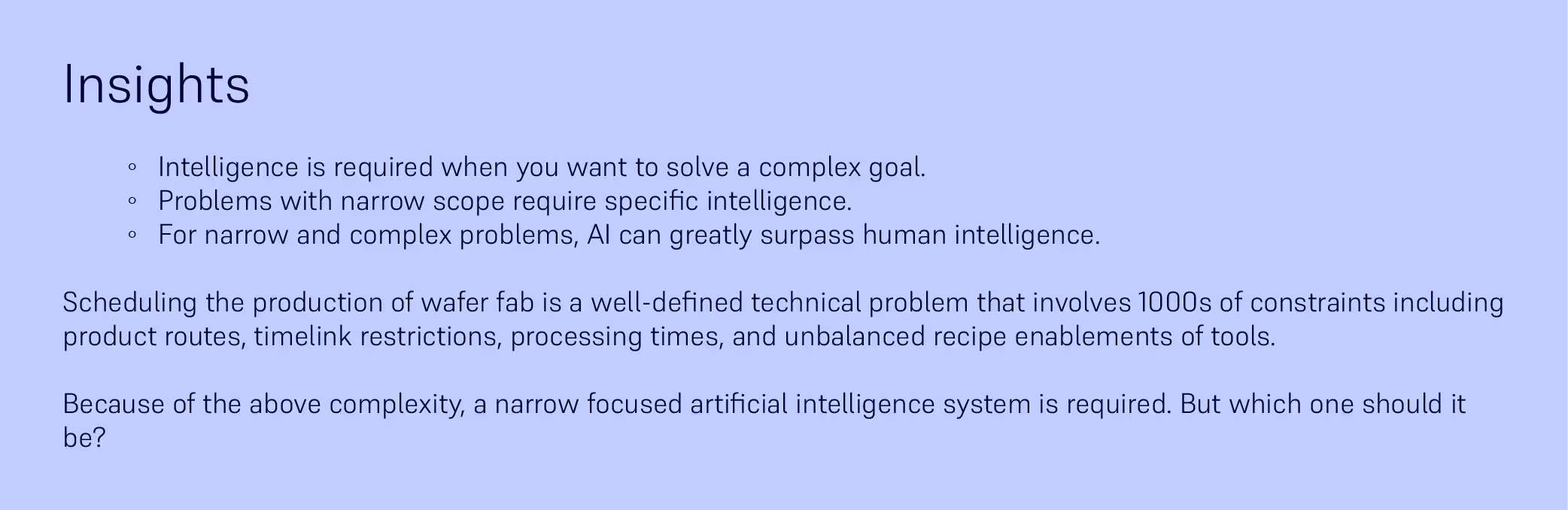
Three important facets of Artificial Intelligence
AI involves creating models and machines that mimic human intelligence, including learning, reasoning, and decision-making.
Learning is an important aspect of AI, relying on a model’s ability to iteratively refine its internal parameters until it can accurately capture underlying patterns. Machine Learning is the cornerstone approach for learning from data and techniques in this category can range from simple models like Linear Regression to complex Deep Learning networks.
Reasoning involves drawing inferences based on established rules and facts, mimicking the human ability to logically connect information. It can aid in tasks like medical diagnosis (See the generative LLM AI from Google Med-Palm 2) or legal case analysis.
Decision-making encompasses action exploration and problem-solving. Action exploration deals with determining actions through interaction with an environment, which can vary from well-defined scenarios, like a chess game, to unstructured situations, like driving a car. Problem-solving, on the other hand, focuses on finding solutions to clearly defined problems with specific objectives and constraints. This can involve simple tasks like sorting or more intricate challenges such as route planning, resource allocation, and scheduling. Optimization and mathematical programming are often employed in these contexts.

Five Crucial Factors When Selecting AI for Production Scheduling
Production scheduling involves making optimal choices to coordinate resources, tasks, and time to meet production goals. It requires handling well-defined parameters and constraints, along with specific objectives like maximising throughput or achieving on-time delivery. As such, it is best suited to rigorous and well-structured AI methods that focus on optimal and feasible decision-making such as mathematical programming.
Nevertheless, good production scheduling can involve some aspects of learning and reasoning as well. Learning can be useful when some of the parameters are not well defined or static. For example, estimating transfer times between different locations of a fab may depend on various parameters, necessitating the use of a prediction model that has learned from past data. In terms of reasoning, a good decision-making approach should allow some degree of introspection from the user. Contrary to black box approaches, such as deep neural networks, mathematically formal methods such as Mixed Integer Linear Programming (MILP) enable transparency and explainability.
Choosing the right AI technique for production scheduling in semiconductor manufacturing involves navigating the intricate balance among five crucial characteristics, each vital in this high-stakes field:
Optimality refers to the ability of an AI technique to reach and prove that the true optimal solution has been found. In a complex environment such as a semiconductor fab, where small improvements can have significant cost or time implications, optimality is of paramount importance.
Feasibility is about ensuring that the solution found truly abides by the constraints of the problem. Semiconductor fabs are bounded by many constraints, including machine capacity, human resources, and time windows. An AI solution must respect these constraints while optimizing the schedule.
Speed is crucial as it directly impacts the responsiveness of the system. Semiconductor manufacturing is a dynamic environment with constantly changing states. Therefore, the selected AI technique must be able to provide fast and accurate solutions to adapt to these changing conditions.
Explainability refers to the ability of an AI technique to provide insights into how it arrived at a given solution. In a high-stakes environment like a semiconductor fab, explainability helps build trust in the system, enables troubleshooting, and allows for more effective human-AI collaboration.
Flexibility refers to the technique’s applicability across a wide range of possible scenarios and system changes. This attribute highlights the capability of an AI method to be fully autonomous and require minimal human supervision and intervention. Within the context of a semiconductor plant, this quality is indispensable, especially as complexity grows and specialised personnel are spread thinner across other functions.
Different AI techniques fare differently on these dimensions. Rule-based systems offer high explainability and feasibility but may lack optimality, especially in complex scenarios. Unforeseen changes in a fab’s state may require rule adjustments or even entirely new ones, affecting flexibility. Heuristic approaches can provide acceptable solutions quickly, but typically cannot provide optimality or feasibility guarantees. Reinforcement learning can potentially offer high levels of optimality and speed, but at the cost of explainability, the risk of infeasibility, and the need for extensive tuning.
In contrast, mathematical programming techniques, such as MILP, can offer an excellent balance. They provide guaranteed feasibility, while the distance to true optimality can be easily computed. They offer explainability in terms of how decisions are made based on the objective function and constraints. Although computational complexity can be an issue, they can greatly benefit from advanced decomposition methods, and are well complemented by heuristic methods [10].
In the context of semiconductor fab scheduling, where feasibility, optimality, and explainability are particularly important, mathematical programming techniques can be a superior choice for AI implementation. Their deterministic nature and the rigour of their mathematical foundations make them a highly reliable and robust choice for such high-stakes, complex operational problems.
Going beyond with AI
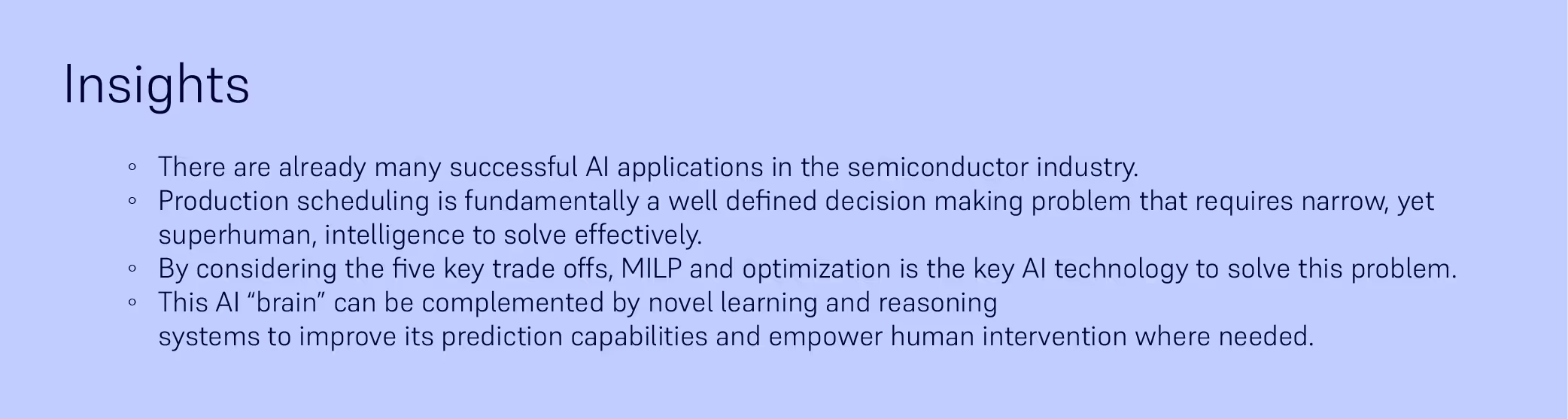
Today, AI in semiconductor manufacturing stands at a critical point. With the increasing complexity of semiconductor processes and the escalating demand for efficiency and quality, the need for effective AI solutions has never been greater. As evidenced in many large companies’ roadmaps, AI is regarded as a key enabling technology of the future [11]. Companies that do not devote resources to a comprehensive AI strategy risk being left behind.
As we delve deeper into the era of AI-driven manufacturing, the nuanced roles of different AI techniques will become more and more apparent. Machine learning approaches bring novel capabilities for learning and predicting from data: yield improvement and predictive maintenance are very promising paths. When it comes to autonomously and reliably scheduling and planning operations in a fab, an exact optimization approach, such as MILP, becomes the key to unlocking peak performance.
Authors:
Ioannis Konstantelos, Principal Optimization Engineer at Flexciton
Dennis Xenos, CTO and Cofounder at Flexciton
References
[1] McKinsey & Company, Scaling AI in the sector that enables it: Lessons for semiconductor-device makers, April 2021. Link
[2] Mönch, L., Uzsoy, R. and Fowler, J.W., 2018. A survey of semiconductor supply chain models part I: semiconductor supply chains, strategic network design, and supply chain simulation. International Journal of Production Research, 56(13), pp.4524-4545.
[3] Lee, T.E., Kim, H.J. and Yu, T.S., 2023. Semiconductor manufacturing automation. In Springer Handbook of Automation (pp. 841-863). Cham: Springer International Publishing.
[4] Mehrdad Mohammadi, Stephane Dauzeres-Peres, Claude Yugma, Maryam Karimi-Mamaghan, 2020, A queue-based aggregation approach for performance evaluation of a production system with AMHS, Computers & Operations Research, Vol. 115, 104838, https://doi.org/10.1016/j.cor.2019.104838
[5] Çınar, Z.M., Abdussalam Nuhu, A., Zeeshan, Q., Korhan, O., Asmael, M. and Safaei, B., 2020. Machine learning in predictive maintenance towards sustainable smart manufacturing in industry 4.0. Sustainability, 12(19), p.8211.
[6] Ishida, T., Nitta, I., Fukuda, D. and Kanazawa, Y., 2019, March. Deep learning-based wafer-map failure pattern recognition framework. In 20th International Symposium on Quality Electronic Design (ISQED) (pp. 291-297). IEEE.
[7] Dreyfus, P.A., Psarommatis, F., May, G. and Kiritsis, D., 2022. Virtual metrology as an approach for product quality estimation in Industry 4.0: a systematic review and integrative conceptual framework. International Journal of Production Research, 60(2), pp.742-765.
[8] Moyne, J., Samantaray, J. and Armacost, M., 2016. Big data capabilities applied to semiconductor manufacturing advanced process control. IEEE transactions on semiconductor manufacturing, 29(4), pp.283-291.
[9] Max Tegmark, Life 3.0, Being human in the age of Artificial Intelligence, 2018
[10] S. Elaoud, R. Williamson, B. E. Sanli and D. Xenos, "Multi-Objective Parallel Batch Scheduling In Wafer Fabs With Job Timelink Constraints," 2021 Winter Simulation Conference (WSC), Phoenix, AZ, USA, 2021, pp. 1-11, doi: 10.1109/WSC52266.2021.9715465.
[11] Bosch, Humans and machines team up in the factory of the future, October 2021. Link
Useful resources
Stay up to date with our latest publications.