Machine Says No – Is There A Way Around The Legacy Equipment Shortage?
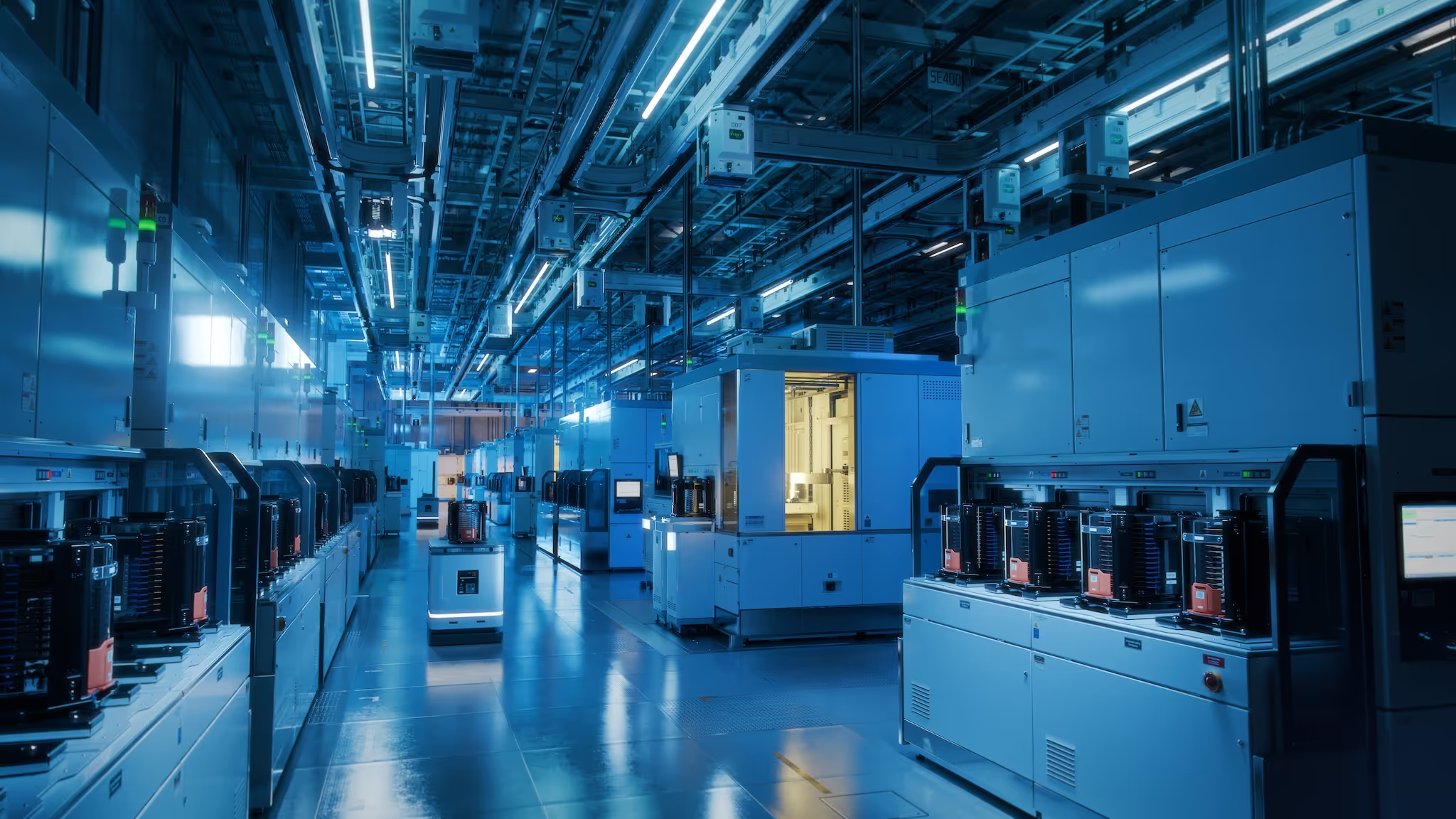
Manufacturing equipment makers are under pressure to meet new fabs’ demands, with a serious knock-on effect for legacy chip makers. But can they increase capacity without increasing their number of tools?
Machines are the new bottleneck
The story of the semiconductor industry right now is dominated by shortages. There’s the chip shortage itself, as global supply chains continue to struggle to meet demand post-COVID. There’s the labour and talent shortage that we looked at in a previous blog. And now hitting the headlines is a manufacturing equipment shortage, with a lead time of up to 18 months on new lithography machines and other chip making tools.
Speaking to Reuters in April, ASML CEO Peter Wennink noted that, not only are the company’s customers having to wait over a year for its products, but that utilisation rates of ASML's machines are also at an all-time high, as semi cos try to keep up with demand. This is borne out by another industry executive, quoted recently by Nikkei Asia, who said, “Chipmakers like TSMC and UMC have told their senior executives to jump on a plane and visit all their key equipment suppliers in the US, Europe and Japan to avoid any of their rivals getting the machines ahead of them, and to personally make sure their equipment vendors are not lying to them about the lead times.”
Yet at least companies like TSMC know that manufacturers are working round the clock to fulfil their orders and provide the machines they need for the new, leading edge fabs they’re building. For many legacy chip makers – whose output is still vital to numerous industries, but is regarded as being on the ‘trailing edge’ of innovation – the problem is more acute, because most equipment manufacturers have actually stopped making the machines they need to increase capacity at their fabs.
The reason why is a simple case of economics. Chip companies around the world are making massive investments in new facilities focused on producing next generation semiconductors, which of course is why there is such a huge demand for machines to service this process. Not only has this created a new and thriving technology ecosystem, but manufacturers can also charge a premium for these machines. In contrast, supplying equipment to legacy chip makers is a lot less lucrative, and in order to meet demand from the new fabs, many manufacturers have simply stopped making the old machines.
The double bind of sourcing equipment
This presents legacy fabs with a major problem. While the focus in the industry is on increasing capacity to meet demand for next-gen chips, semiconductor shortages are occurring across all sectors, with markets such as traditional, non-electric automotive still reliant on older, legacy chipsets. As such, there is increased demand at legacy fabs as well, with companies dependent on machines that should have already been retired because there aren’t new replacements for them anymore. This also means that if a legacy fab wants to ramp up production, it has to source and recondition second-hand equipment, which is both increasingly difficult and far from ideal.
However, there’s another issue that affects companies with legacy fabs that want to boost capacity, and that’s one of increased costs. Because these facilities have been operating for a comparatively long period of time, they will almost certainly be fully depreciated, which is reflected in the price of the chips they manufacture - in other words, because their capex costs are now low, chips can be sold more cheaply than when the facility was still being paid for and capex had to be factored into the price. But this means that, even if a company manages to source additional machines, its capex will go up again, which will potentially make its chips more expensive and less competitive.
Legacy chip companies are thus caught between a rock and a hard place. On the one hand, they’re finding it increasingly difficult to source new tools to produce more chips. On the other hand, they risk becoming uncompetitive if, by increasing capacity with new machines, they are forced to increase their prices. And while using depreciated second-hand equipment is an option to get around this, finding it is another matter.
This is a huge headache for legacy fabs, but the impact in the wider world is even worse, with many industries continuing to suffer from chip shortage issues because their suppliers are unable to ramp up production.
Increase capacity, not machine count
There is another solution which bypasses the vicious circle described above, and that’s for companies to embrace smart manufacturing practices. Historically, the favoured way to significantly expand capacity was to increase the number of machines in the fab, and many companies are still wedded to this way of thinking. But advances in production scheduling software, in particular, are enabling forward-thinking companies to unlock capacity they didn’t know they had by optimising their WIP and the way their machines are used.
Most legacy fabs still use heuristics-based scheduling software to run their WIP, derived from SLIM methodology. However, this methodology is now over 20 years old, and was developed to work within constraints that no longer exist. Access to computational power - driven by cloud computing - has increased enormously, which means that much more sophisticated scheduling systems can now be used to make decisions about the WIP.
By using complex mathematical algorithms, this new generation of scheduling systems can make production decisions that are optimal for that exact point in time, enabling fabs to work at genuine capacity rather than the ‘false capacity’ that an over-reliance on rules-based software has created. The results that we have seen are truly game-changing, with capacity increases of up to 10% using the same number of machines and tools.
Rather than getting caught up in the equipment bottleneck, another solution exists today that can be quickly implemented with minimal upfront costs. By optimising production scheduling with AI-based precision, makers of legacy chips can increase capacity and meet new orders without having to expand their physical facilities. In a world of ongoing shortages, that’s a significant advantage.
Useful resources
Stay up to date with our latest publications.