Scheduling as a Cornerstone of the Smart Factory [Part 2]
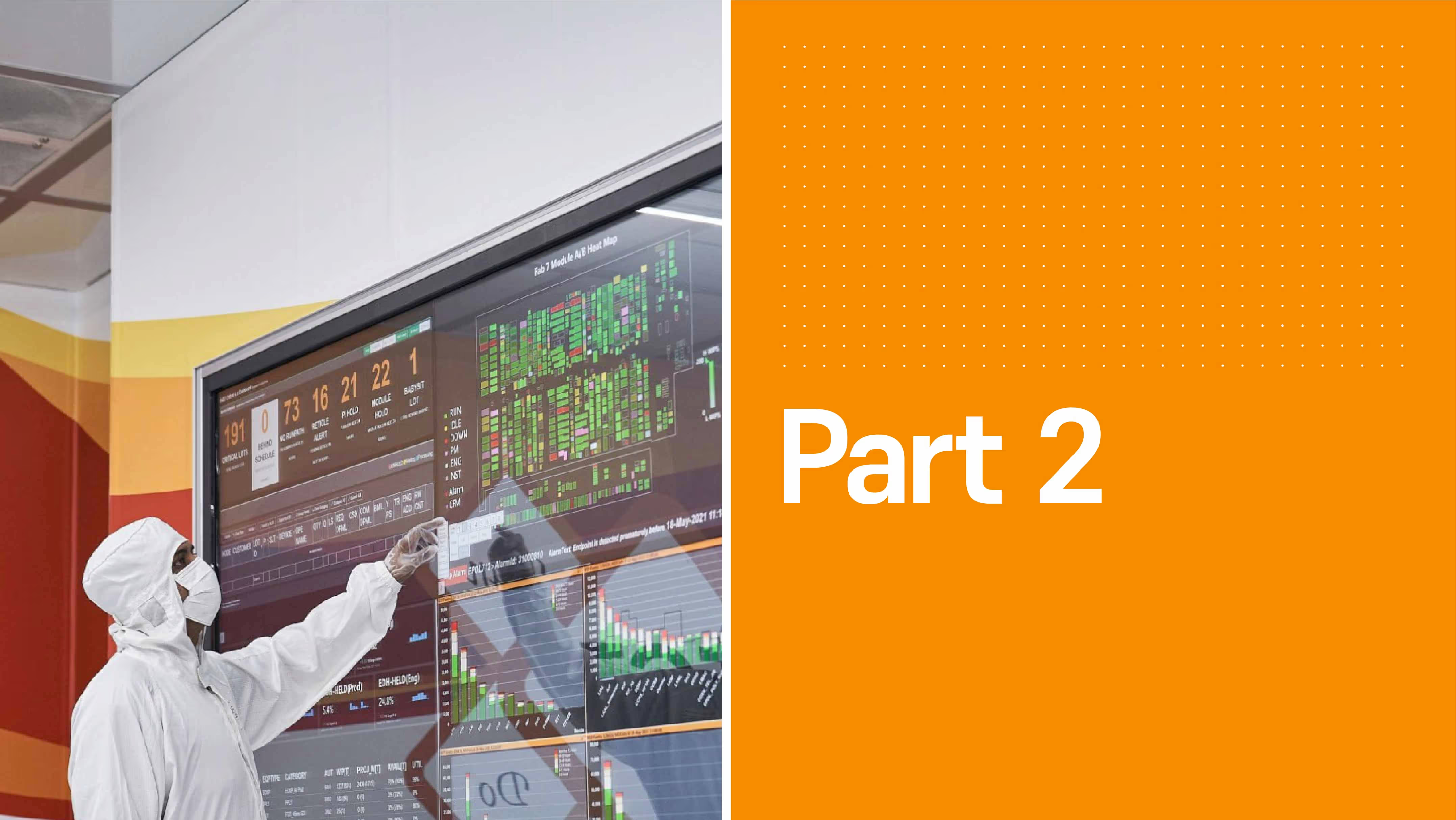
In Part 1 of this blog, we focused on use cases where lots are scheduled on tools and how advanced scheduling gives users the ability to optimize for future decisions as well as real-time. When we say "advanced," we are referring to autonomous, optimization-based solutions. Our emphasis was primarily on how scheduling can enhance productivity in a fab today. In Part 2, however, we’ll delve further into its potential for fabs in the not too distant future.
Previously, I discussed how task lists are typically associated with human workers. However, it is worth noting that task lists can also be applied to automated systems such as automated guided vehicles (AGVs) and automated material handling systems (AMHS) with the use of an advanced scheduler. With task lists, an advanced scheduler can not only determine which lot is assigned to which tool and when, but also which operator – or robot – will be serving the tool. There’s a whole set of new opportunities that arise with that, as humans and robots, just like tools, have a limited capacity that can be optimally utilised. It’s clear then that the possibilities for advanced scheduling go beyond the stand-alone Industry 4.0 applications and have the potential to integrate vast amounts of fab data into a holistic system.
One of the use cases of such a holistic system is described later on in this blog as a type of ‘digital twin’, but the capabilities of an advanced scheduling system go beyond that. With a digital twin concept, the human is still very much inside the cockpit. An advanced scheduling system, on the other hand, is more like an autopilot, augmenting the capabilities of other systems and taking control of manufacturing decisions when necessary. As such, advanced scheduling is a cornerstone of the so-called ‘smart factory’. Let’s try to understand the huge array of benefits it can bring. First, we’ll cover a couple of use cases that can benefit the manufacturers. Second, we’ll share some thoughts on how advanced scheduling aligns with the idea behind Industry 5.0 and how the technology can serve ourselves as humans.
- WIP Transport Scheduling
Once a lot is intelligently scheduled, we know when to process it and on which tool. The lot can be transported to that tool’s specific staging rack just before it gets processed. It enables fabs to eliminate waste by optimizing transport capacity, which removes the likelihood of a lot being transported at half capacity only for it to wait in queue. Transport scheduling also enables splitting logistics and processing workflows; some workers focus on keeping the tools running, others focus on getting the lots to the tools in time. Multi-cleanroom fabs will make better use of their capacity in areas that for logistical reasons are not preferred. Which means no more remote idle machines waiting for a lot that doesn’t arrive.
- Dynamic Capacity Models
With better control of lot processing, intra-fab logistics, and workforce planning, we get a more realistic view on the true capacity of a factory. We call it a dynamic capacity model, resembling the idea of a digital twin of a production plant. A dynamic capacity model better reflects the current state, loading and dynamics in a factory, as opposed to the static capacity models commonly used. Until now in wafer fabs, dynamic capacity models have at best been approximated by what-if scenarios in simulation models, but the potential goes beyond that. When playing around with different scenarios – e.g. when to plan maintenance or shutdowns, which availability increase has the most impact on the whole factory, what’s the effect of frequent product mix changes, what lead times to expect and so on – it should allow factories to better judge the impact of their decisions. Optimization can even help by not only interpreting the outcome, but suggesting the best decision for a fab’s goals.
- Multi-factory Models & Supply Chain Planning
Eventually, dynamic capacity models could scale to corporate level in multi-factory models. Further up, these models could feed into supply chain planning software. During the supply chain crisis, it was striking to see how disconnected sales and operations planning cycles in semiconductors were from the actual operational challenges of factories. Part of it was because of models that don’t properly comprehend the actual situation the factory was in. Fabs were treated as black boxes with a simple input and output signal, but just because you have promised your customers a sooner delivery date, it doesn’t mean it will happen automatically. You need a driver towards that new target, and that’s where advanced scheduling software helps, by optimizing towards shorter lead times. Its integration into dynamic capacity models and supply chain planning software would lead to more reliable input for inventory and order fulfilment optimization engines. This translates into lower inventory costs and better delivery performance of a company.
Eventually, we want technology to help us overcome the challenges we face as humans. From what has been written so far, this blog might give the impression that this technology is primarily serving profitability. But becoming a smart factory doesn’t necessarily contradict with a human-centric approach. Industry 5.0 is the theoretical concept that’s been introduced for that. It counters the illusion that the future of manufacturing is one in which humans play a minor role. Instead, we should embrace both the capabilities of new technologies, as well as those of humans and find synergies to make the best of both worlds. While Industry 4.0 can do a great job in automating repetitive tasks or making sense out of masses of data, humans have the advantage of better interpretation of context, require fewer data points to understand, and can make value trade-offs. Humans will not miraculously disappear from the factory shop floor, so we’ll benefit from thinking about how these advanced technologies can harmoniously coexist with people and yield mutually beneficial outcomes.
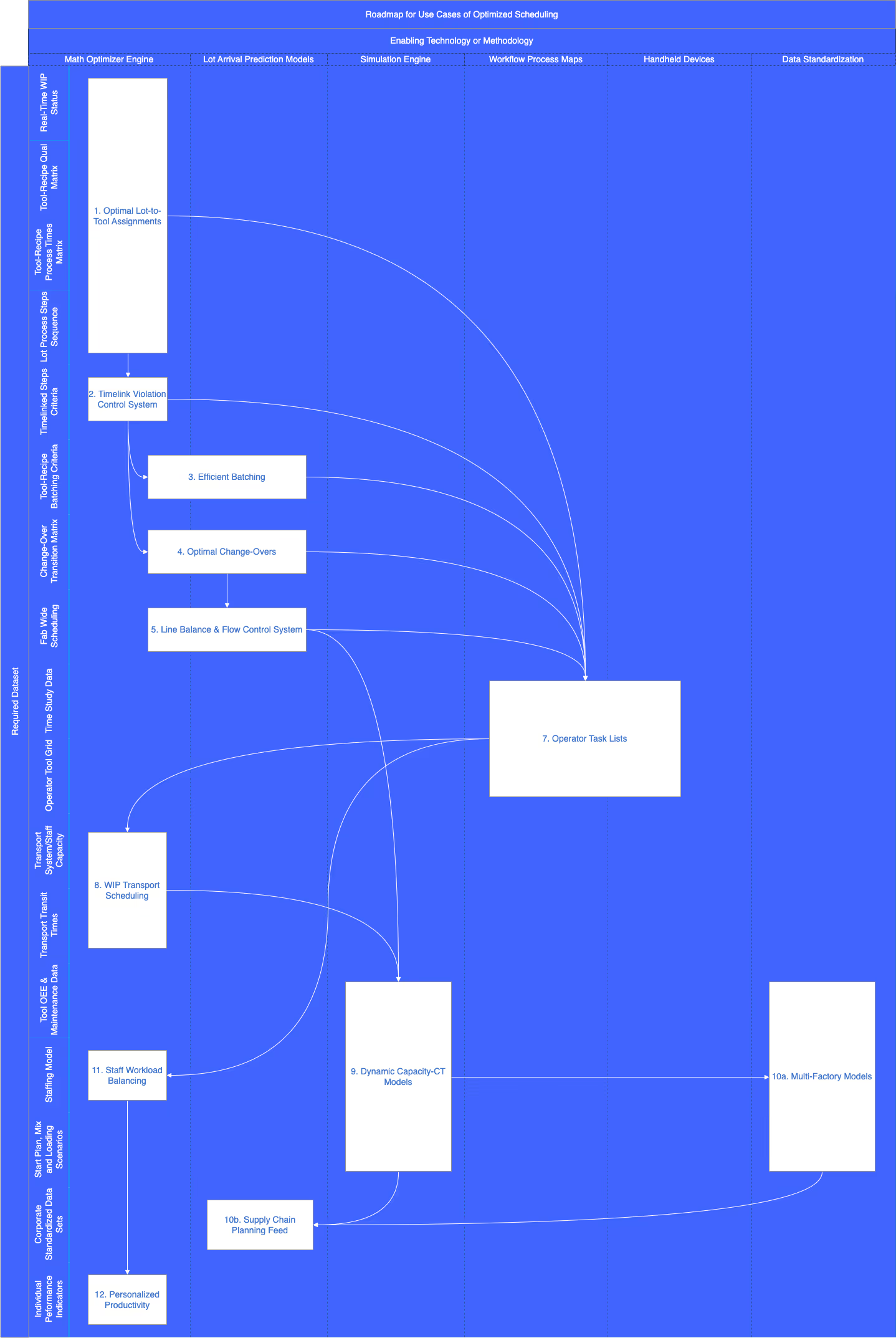
- Staff Workload Balancing
The obvious fear with advanced scheduling is that operators and technicians will turn into de facto robots, where only adherence is of importance when aiming to get more out of the workforce. Let’s turn that thought up-side-down: what if the same work could be better distributed amongst the team by offloading peaks to underloaded co-workers? Advanced scheduling can better predict and hence properly distribute work aligned with an individual's availability and level of training. Also the workflow itself - the number and order of actions to perform - can be streamlined to lower physical and mental workload.
- Training, Evaluation & Individual Productivity
With detailed production schedules, any lack of staff or training becomes directly visible and quantifiable. Hiring and training programs could become more timely and data-driven, just as annual evaluations will become less subject to biases of the manager. Even on-the-spot productivity can be monitored and optimised. This may sound like a “Big Brother” concept, but compare it with the advancement of sports analytics and medicine in the last decade. Professional athletes don’t complain about data integrity and privacy issues, because (1) it’s part of their job and (2) it helps them in what they want to achieve. If athletes ignore their data, they simply don’t reach the top anymore. Similarly, the fourth and fifth industrial revolution will bring staffing to higher levels of productivity, not because they are squeezed out more, but because the data will reveal where there’s room for improvement or when a red line is about to be crossed.
Given the increasing scale and complexity described above, significant computational power and data storage capabilities will be necessary. This makes it likely that cloud-based technology will be adopted to facilitate the transition to smart factories. Although many fabs are currently far from achieving smart factory status, it is clear that the industry is moving in this direction. Therefore, factory managers must acknowledge that the transition to becoming a smart factory is not just a concern for the future and must be implemented within a realistic timeframe. The foundations for this transition, including employee readiness, are already being established today. And given the use cases discussed, let there be no doubt that advanced scheduling will play an integral part in the next generation of wafer fabs.
Author: Ben Van Damme, Industrial Engineer and Business Consultant
Useful resources
Stay up to date with our latest publications.