Position Vacant: Are Chip Companies Really Running Out Of People?
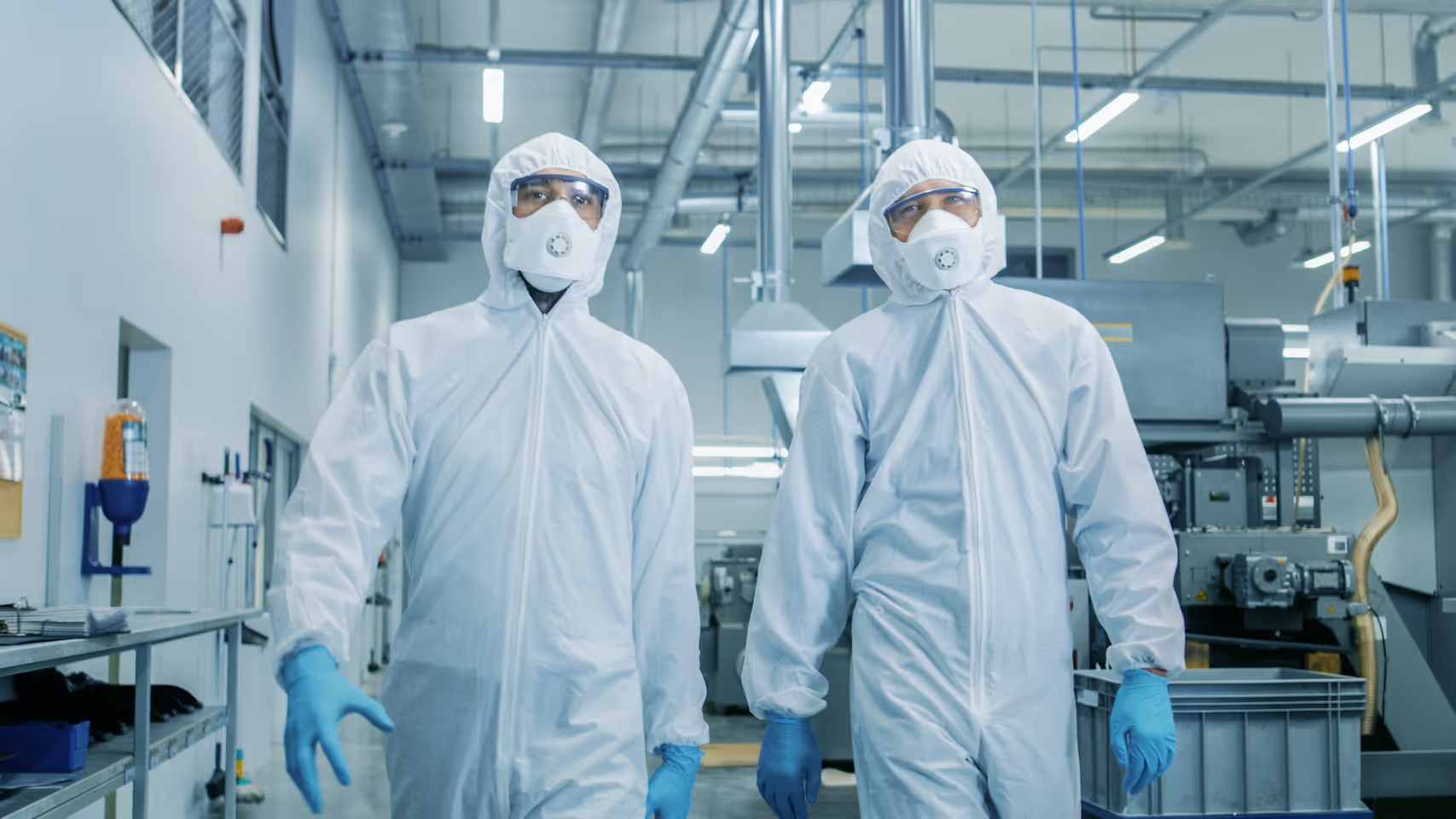
The semiconductor industry worries that it won’t have enough workers to run its new fabs. But there’s a labour problem right now at legacy facilities. Could disruptive technologies help to solve this problem?
A worldwide labour crisis
It’s not just supply chain issues that are afflicting the semiconductor industry. Another major problem is a shortage of labour. There’s a significant fab building programme underway, but already companies fear there won’t be enough manpower to run them properly.
This is a worldwide issue. A recent white paper by talent management company Eightfold shows that, to meet the capacity demands from new fabs, the US chip industry needs to increase its workforce by at least 50%. And according to Deloitte, China is also facing a labour crisis, with 400,000 more semiconductor employees required to meet its stated targets. Even Taiwan is feeling the pinch, with a huge gap opening up between rocketing demand and the ability to meet it due to a lack of skilled engineers.
Unsurprisingly, these countries are doing everything they can to boost the number of STEM graduates, with billions of dollars going into universities to support this goal. In addition, the SEMI Foundation – the non-profit arm of global industry association SEMI – has a number of programmes in place to develop a larger and more diverse workforce, with the ultimate aim to dramatically expand the pipeline of skilled workers ready to fill labour deficits.
However, while these initiatives are laudable and entirely necessary, they don’t address the labour issues that many legacy fabs are facing right now. These issues – such as experienced operators retiring and skilled engineers being poached by newer, bigger facilities – mean that it’s growing ever harder for legacy fabs to meet capacity pressures. With their workforces dwindling or under threat, what can be done to ensure that legacy fabs are still able to operate efficiently?
The problem of running fabs on gut feeling
One solution is to change the way in which fabs operate. Many legacy facilities are still reliant on workers on the floor to move WIP from one machine to the next, since upgrading legacy fabs to facilitate advanced material handling systems (AMHS) is often too costly or too complicated. Instead, operators tend to take instructions from a rules-based scheduling software. However, in some instances the operators will make their own scheduling decisions based on their ‘gut feeling’ if, for example, the system doesn’t take into account certain constraints and makes an implausible suggestion or the operator thinks they can make a better decision themselves.
Because of the lack of intelligence in rules-based scheduling systems, many chip companies have to rely on experienced, highly-skilled operators to oversee the manufacturing process. Therefore, when companies look to expand facilities or replace employees, they understandably think they need to find operators experienced enough that they require minimal training to adapt to their fab – and worry that new candidates don’t exist in sufficient quantity.
However, if decision-making around scheduling in the fab can be improved, with less dependence on operators’ own judgements, then it’s possible to not onboard new staff much quicker but also optimize the total number of people needed to run the facility.
The simple rules-based scheduling software that many fabs rely on to guide operators’ decisions runs using predefined rules. These predefined rules take into consideration only a limited number of possible cases, resulting in the software making suboptimal decisions when it is faced with unknown scenarios which contribute to inconsistent results. Little wonder then that experienced operators often believe their own scheduling decisions are just as good, if not better. But by applying smart manufacturing practices – as SEMI is encouraging chip companies to do – it’s possible to automate and optimize production scheduling and easily add constraints that allow for far better decision making.
The AI-driven production scheduling system can analyse the state of the fab at any given moment and make scheduling decisions that are optimal for that precise point in time. The ramifications of these systems are profound. If the WIP flow is truly optimized, there is no need for operators to make their own dispatching decisions – they just need to follow the instructions coming from a smart scheduler, reducing the pressure on fabs to find highly skilled workers and enabling a concomitant percentage reduction of the manpower required on the fab’s floor. Optimized scheduling also allows for significant improvements in production KPIs such as throughput and cycle time – assisting a fab to achieve overall performance gains.
In addition, optimized scheduling removes the need for skilled engineers to spend time analysing production data in an effort to continually tweak the rules and maintain the scheduling system. Instead, their time can more usefully be spent on other tasks. Essentially, optimization enables more to be done with less.
Why competition is sometimes counter-productive
Another area in which advanced technologies can have a positive impact on the labour issue - not just in legacy facilities but across the industry - is in the optimization of manufacturing. At every semiconductor company, a significant proportion of their engineering talent is focused on developing ways to improve the chip production process, and thus gain an advantage over their rivals. While this type of competition undoubtedly drives progress within the industry, it can also be counter-productive, with teams at each company tied up trying to solve the same problem.
It's only natural that a cutting edge industry structured around research and science should assume the best solutions to every problem can be developed internally. Yet this is not always the case, particularly in emerging fields such as advanced AI. Rather than tie up talent and resources trying to solve issues such as optimizing scheduling in fabs, companies should be prepared to investigate ‘disruptive’ technologies from beyond their own walls that may already have cracked this problem.
By adopting a ‘best-in-class technology’ approach to the manufacturing process – rather than perpetuate a culture of trying to develop proprietary solutions for everything – companies can instead refocus their engineering talent on core competencies. For instance, by embracing external innovation, chip companies can redeploy internal teams to overcome efficiency obstacles elsewhere in the fab that they previously did not have the capacity to work on.
It goes without saying that continuing to promote STEM-based graduates towards careers in microelectronics is vital if the semiconductor industry is to meet its ambitious targets over the next decade. But while disruptive technologies can’t make the current labour shortage problem go away on their own, they can make a serious contribution to lessening its impact and changing chip companies’ attitudes towards recruitment.
Useful resources
Stay up to date with our latest publications.