User-focused Digitalisation: Empowering Wafer Fab Operators with Intelligent Software
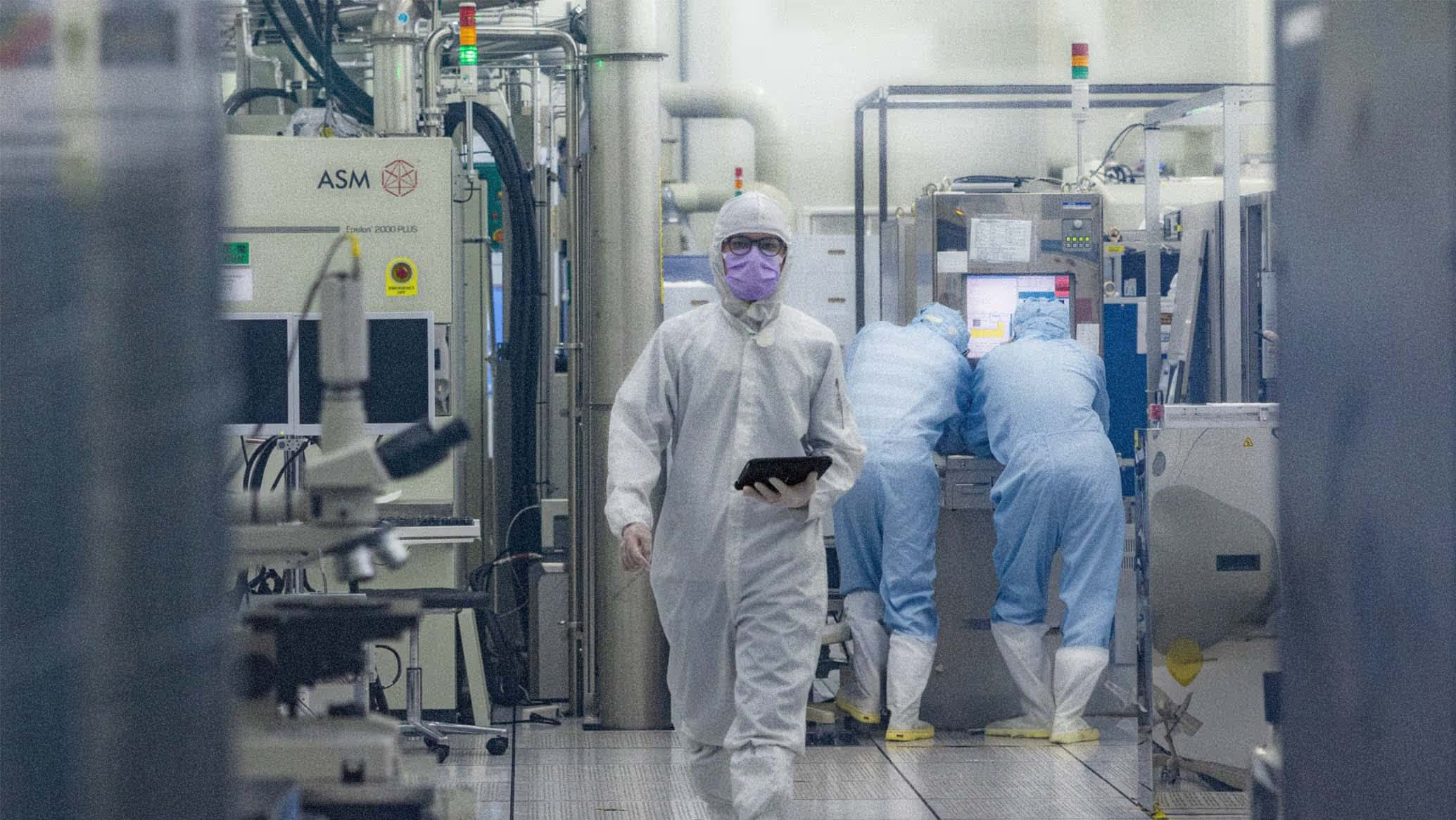
For many years, my career has been deeply rooted in the ever-changing world of manufacturing–an industry where progress relies on innovation. Throughout my professional journey, I have been immersed in this dynamic sector, focusing on creating bespoke software solutions for manufacturing and logistics, all the while seamlessly integrating third-party solutions into established workflows. My experience has afforded me the opportunity to first-hand witness the profound changes that digitalisation and automation have brought to the manufacturing landscape. As technology and manufacturing processes have become more closely intertwined, the operational dynamics of production have been reshaped.
Like any successful partnership, the marriage of manufacturing and technology requires a strong foundation built on trust, mutual understanding, respect, and a shared ambition to support each other's growth and empowerment. However, these transformative shifts have brought along their fair share of challenges and concerns that continue to echo around the manufacturing world.
Embracing servant software in the manufacturing landscape
A few years ago, I collaborated with a couple of value stream managers as we scoured the market for various digital products, seeking the optimal solution to integrate with our in-house developed material requirements planning (MRP) system.
One significant concern was the fear of adopting software that was too intrusive. In an industry where precision and control are paramount, the idea of software delving too deeply into our operations was disconcerting. Even worse was the fear of getting locked into specific technologies. Having deeply integrated software within our operations poses a risk due to them being so costly to replace, which potentially limits our capacity to adapt and evolve in tandem with the industry. We wanted automation and the ability to forecast the incoming work. Our aim was to prevent defects and misjudgments, all the while ensuring that we retained control over our manufacturing processes. And importantly, we were adamant about not compromising our quality standards.
The reality is that the market for manufacturing-oriented software is littered with solutions that are cumbersome, inflexible, and expensive. When I joined Flexciton as a Senior Product Manager, I was pleasantly surprised to discover a refreshing departure from the norm in Flexciton's product philosophy.
It evokes the concept of “servant software”. Similar to the idea of servant leadership–where a leader prioritises the well-being, growth and empowerment of team members–servant software aims to streamline processes, simplify tasks, and provide solutions that cater to the users' requirements and preferences.
A servant software encompasses, as a foundational principle, the advantage of being as flexible and adaptable as a meticulously tailored suit. This quote summarises the concept:
Upgrade your user, not your product. Don’t build better cameras — build better photographers.
— Kathy Sierra
In the challenge of digitising semiconductor wafer fabs, Flexciton aspires to play a pivotal role in cultivating highly skilled operators and managers—individuals who are empowered by our technology rather than being replaced by it.
Automation for enrichment, not alienation
Picture Josh, a Senior Fab Operator in the diffusion area, who has been working for five years in a manually operated wafer fab. Half of his workday is consumed by the arduous task of sifting through a colossal spreadsheet that meticulously logs all the lots in progress, each with its own unique characteristics. He sits at his desk, constantly toggling between this spreadsheet and another monitor displaying the real-time status of the tools.
Jotting down notes on a piece of paper, Josh ventures into the tangible world of the fab. There, he confronts the actual events unfolding. He asks himself, "Is this an actuality? Are these lots genuinely ready for processing? Can I really preload this tool?" Realisation strikes: "No, they are still in transit, and I cannot proceed with this batch," or "I can’t preload this tool yet; a few minutes are still left." Josh retreats to his desk to recalibrate his plans once more.
When operators are liberated from repetitive and inefficient tasks, they can harness their cognitive abilities to identify improvement opportunities, propose innovative solutions, and implement process enhancements directing their efforts towards value-added activities that demand uniquely human qualities. This empowerment not only enhances job satisfaction but also drives a culture of ownership and accountability.
Embracing Lean Management principles
Servant software aligns seamlessly with the principles of lean management, a philosophy that champions efficiency through the elimination of waste and continuous improvement. Lean management is not just about operational optimization, it emphasises a shift in mindset, encouraging all levels of an organisation to work cohesively towards shared objectives. By integrating servant software within this framework, manufacturers can elevate their workforce's role away from simply executing tasks and towards contributing to the bigger picture.
Operators typically concentrate their efforts within their designated areas of responsibility, striving to optimize operations by carefully managing various tasks. They work diligently to maintain a delicate balance among tools, ensuring workloads are efficiently allocated, changeovers are optimized, and maintenance and process control activities are accommodated for. Even within a confined production area, this manual juggling of numerous constraints and variables presents a considerable challenge, a topic we explored further in our article on autonomous scheduling.
A new way to schedule the fab is the key. But what’s in it for the operators? What is the impact on their daily work? Our software aims to provide operators with a tool that leads them to take the right action at precisely the right moment. It ensures that tasks are executed with impeccable timing, neither prematurely nor delayed, considering not only the current status of the WIP (work in progress) and the tools they are responsible for, but also the potential effect of their actions on the following production stages.
This goes beyond optimizing individual areas; instead, it is designed to harmonise the entire manufacturing process. By avoiding over-optimization of one area, we prevent potential bottlenecks or resource shortages elsewhere in the workflow, resulting in a balanced, easily monitored, and controllable production process.
The fab in your pocket!
Our operators' tools are integral to the Flexciton application ecosystem, where every component is integrated and consistent. From analytics and scheduling to automated tuning, and extending to the practical, hands-on actions of our operators—such as loading or unloading tools or conducting Statistical Process Control (SPC) tasks—our system comprehensively covers all aspects. Therefore, Josh can simply glance at his portable device to discern the next best action to perform or be notified when something urgently requires his attention.
Our primary goal is to provide operators with the essential information they need, without overwhelming them. This information is easily accessible on portable devices, ensuring its effectiveness from the very first day an operator steps into the fab.
Operators—now armed with useful insights and empowered by automation—can expand their contributions beyond their individual roles, engaging in more value-adding tasks. The result is a collaborative ecosystem where every individual becomes a key player in achieving fab-wide targets and goals.
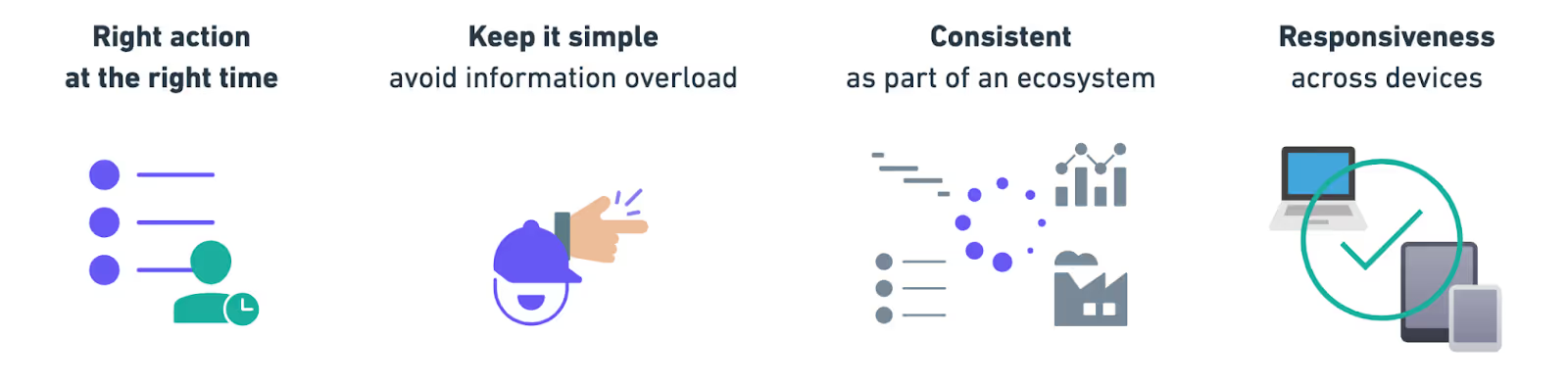
A customer-centric product philosophy
In delivering software solutions for the semiconductor industry, our mission revolves around achieving an optimal balance, thereby cultivating a modern, flexible, and customer-centric product philosophy. Our platform, while robust, maintains a deep respect for operational boundaries, ensuring that our customers are not confined to rigid models.
Instead, it functions as a dynamic tool that enriches adaptability and innovation, and grants users complete control over their manufacturing processes. By adhering to these core principles and relentlessly pursuing software that empowers without overwhelming, we unlock the full potential of a harmonious synergy between technology and manufacturing, propelling progress forward without concessions.
Author: Valentina Vivian, Senior Product Manager at Flexciton
Useful resources
Stay up to date with our latest publications.