Is It Possible to Improve Performance and Be More Energy Efficient?
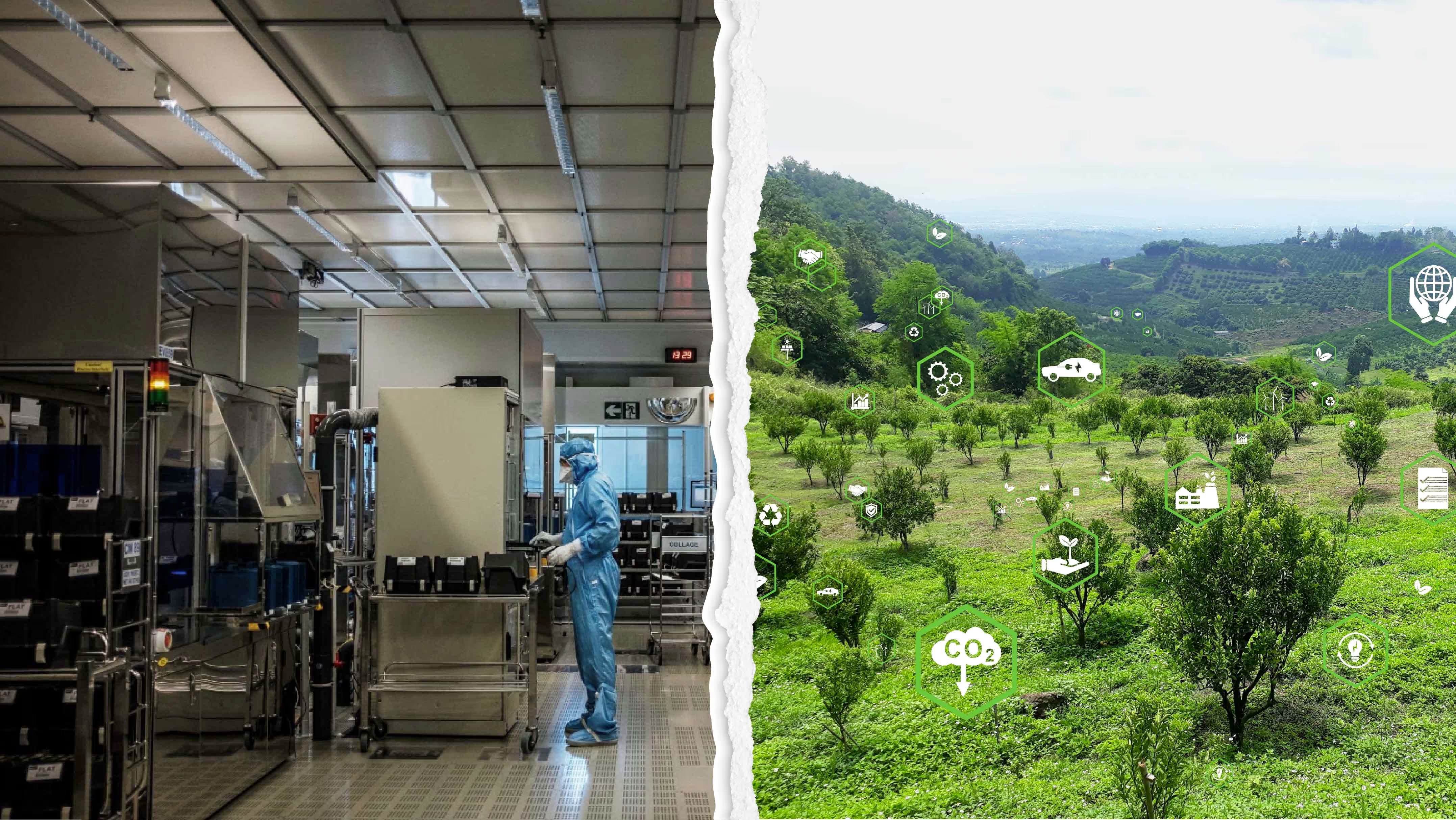
The semiconductor industry needs to become more sustainable in a world of increasing demand – optimization holds the key.
An energy-intensive industry
Over the past decade, industries worldwide have had to tackle the issue of sustainability as a matter of increasing urgency, with the need to mitigate greenhouse gas emissions becoming a major factor in companies’ operations and processes. For many, this has been a difficult accommodation to make, because it has forced them to change the way they work. On the other hand, addressing the climate crisis has acted as a catalyst for the transition to more innovative and efficient methods of production and manufacture.
The semiconductor industry is at the heart of our modern technological society, and as recent supply chain issues have demonstrated, any slowdown in production has a significant knock-on effect on multiple other sectors. Given its centrality, and the need to maintain output, sustainability hasn’t always been as high on the agenda of chip companies as it should have been. However, ignoring the serious environmental impact that semiconductor industry has on the world around it is no longer tenable.
According to McKinsey, “large semiconductor fabs use as much as 100 megawatt-hours of energy each hour, which is more than many automotive plants or oil refineries do.” They also point out that an average fab will use as much power in a year as 50,000 homes – that’s enough electricity to run a small town. And as the demand for semiconductors continues to grow, and the production process becomes ever more sophisticated, on its current trajectory, the industry’s energy usage is only set to increase.
Electricity production is of course a major source of CO2 emissions, with the majority of power stations still fuelled by hydrocarbons such as coal and gas. It’s an inescapable fact that using more energy means emitting more greenhouse gases – so reducing energy consumption is an obvious way for the semiconductor industry to improve its environmental footprint. But given the demand outlined above, how is this realistically possible?
KPIs vs the green agenda
If we look at where the energy in fabs is actually being used, a solution becomes clearer. McKinsey calculates that approximately 55% of energy consumption is generated by running tools. Given that many of the machines on a fab’s production line are in use 24/7, this perhaps isn’t that surprising. And as I noted earlier, chip companies aren’t about to reduce this level of operation just to become more environmentally-friendly – for both them and other industries, the stakes are too high to do anything that would threaten production.
This is reflected in the KPIs that fabs work to, which are primarily based on cycle time, throughput and yield – energy consumption has historically been very much a secondary consideration. However, production doesn’t completely exist in a bubble, and as with any company, the bottom line is the ultimate driver of operations. Cost reduction is just as important as revenue generation. McKinsey notes that, depending on local electricity tariffs, energy consumption can account for up to 30% of a fab’s operating costs. And with the price of energy continuing to rocket, that figure is almost certain to increase.
So given that energy is a factor that affects both production costs and sustainability, reducing consumption is edging its way up the fab’s table of priorities. Yet what if you could address both those primary KPIs and the need to be greener at the same time?
Optimizing primary goals and energy consumption
Optimization technology is the key. It’s a point I keep returning to, but if chip companies are to deal with the challenges that the future is sure to keep throwing at them, then they have to start adopting best-in-class smart manufacturing practices and software.
To properly optimize the way in which the fab works, we have to first understand exactly what the state of the entire WIP is in real time. By mapping the current state of the fab’s operations, it’s possible to identify where bottlenecks are occurring due to sub-optimal scheduling. And in our experience of working with different fabs, the tools where queues usually occur are involved in the most energy-intensive stages of the production process – for example, photolithography, diffusion furnace and in the cleanroom.
Using optimization software to reduce bottlenecks by improving how wafers move through energy-intensive tools, the fab’s primary KPIs can be met and energy consumption at these tools can be reduced. For example, doing more moves with fewer tools at the photo stage means that it’s possible for some tools to be left idle. Or doing the same moves but with fewer batches at the furnace stage means fewer energy-intensive furnace runs.
At the tail end of last year, I gave a presentation at the Smart & Green Manufacturing Summit, as part of Semicon Europa 2022, that outlined how our scheduling optimization software has already achieved these goals in the real world.
Optimization technology can also be used to directly control the energy consumption of less busy tools as well. As long as those areas that are prone to bottlenecks are running efficiently, and all primary KPIs are being met, tools in other areas can be optimized specifically for energy conservation – for instance, powered down because the scheduling technology has identified that they aren’t required or don’t have to be operated at their maximum rate.
Taking sustainability seriously
Most of the larger semiconductor companies are looking at ways to be greener and meet net zero goals, although carbon offsetting is currently playing more of a role than making manufacturing processes more energy efficient. However, some companies are addressing the issue head-on and looking at ways to control their fabs’ energy use – for example, Flexciton, Imperial College London and the Technical University of Munich are currently working together on a project to map Infineon’s energy consumption, with the aim to better understand how smarter decisions can help the company reduce its carbon emissions.
The demand for semiconductors is only going to grow in the decades ahead, but a reckoning over the industry’s attitude to sustainability will be reached much sooner than that unless energy reduction becomes one of its key priorities. Yet by working smarter and re-evaluating their production processes, it’s absolutely possible for companies to improve throughput and yield while at the same time being more energy efficient.
Author: Jamie Potter, CEO and Cofounder
Useful resources
Stay up to date with our latest publications.