Managing The Human Side Of Smart Manufacturing
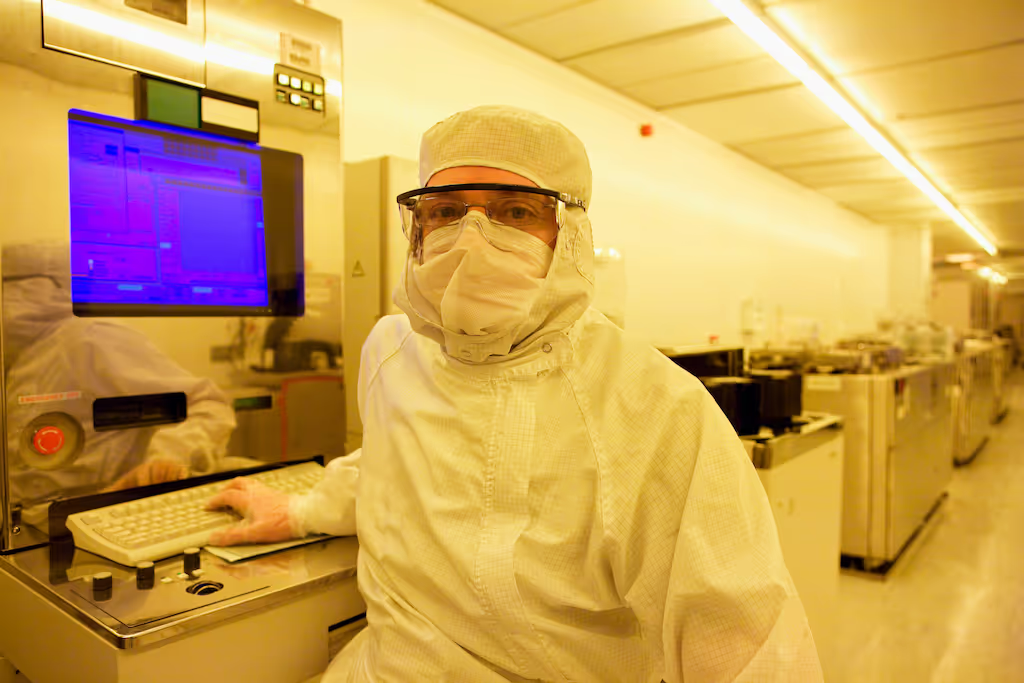
Change management is just as important as new technology in a successful implementation.
People have the power
The core belief that drives the work we do here at Flexciton is that, for the semiconductor industry to advance to the next level of efficiency, it has to comprehensively embrace smart manufacturing practices.
As I’ve written previously, the rollout of smart manufacturing will require fabs to adopt ‘disruptive’ cloud-based, AI-driven technologies. As such, the move to smart manufacturing will be an absolute step change for most companies and will result in some fundamental adjustments to the way that the fab works. Yet ensuring that these new technologies integrate seamlessly with the existing systems is only part of the challenge.
Ultimately, the success of a smart manufacturing implementation will be decided by the people who work in the fab. For these new technologies to deliver the efficiencies they promise, there has to be total buy-in from the staff who are expected to work with them, particularly in legacy fabs where final decisions are still often made by humans. This is what we call the human side of smart manufacturing, and getting it right is just as important as deploying the technology itself.
What exactly is the human side? It’s the recognition that, for all the advanced tools and machinery, and the software that runs them, most fabs still depend on skilled workers to not only move the WIP around the factory floor, but also make decisions that are integral to the manufacturing process itself. As such, these workers are deeply invested in how the fab runs and take pride in the job they do.
Sensitive change management is critical
For implementation of smart technology to succeed, the human side of the transition has to be managed with skill, sensitivity and awareness. It’s not easy to shift existing work practices in any industry, and this is particularly the case within the semiconductor sector, which is used to doing things its own way.
Cutting-edge disruptive technologies are more often than not born in the minds of academics who, despite offering an innovative solution, may have a limited understanding of the inner workings of a fab. As a result, they can fail to take into account the complex implications of their technology and how the adoption phase can impact the people working with it. This is one of the reasons why fabs tend to stick with implementing conventional or in-house solutions. Despite being far less sophisticated, these technologies are built with an appreciation of the realities of a factory and the people who work there. Subsequently, the adoption process is smoother and, although it may not provide radical performance improvements, the impact can be more positive for the fab and its workers.
The key point here then is that, in order for a disruptive smart technology to be implemented successfully, it is critical to have a comprehensive understanding of a fab and a sensitive approach to human change management. Resistance to change is only natural and is to be expected, which is why from the word go, we work side-by-side with our clients to ensure that everybody is on board with changes to the way the fab works, because new technology on its own is not a silver bullet. Fabs don’t conform to theoretical models, but are subject to all manner of real world influences, with the human factor being especially strong.
The Flexciton approach
There are specific steps that we take to make the change management process as successful as possible:
Understand their challenges
To support the change management process, we build close relationships with our clients – not only to create trust, but also to develop a deep understanding of how their current processes work and how production has been executed so far. We have to identify both the objectives and ambitions of the management and the specific challenges and pain points that operators are facing on the shop floor. We do this by shadowing the roles of everyone at the fab who will be affected by the new implementation.
Educate and explain
Change management must follow a systematic methodology, but every fab is different, and so there’s no such thing as a standardised rollout. We understand that our technology will change the way in which both operators and engineers work, which is why the onus is on us to educate and explain why these changes are necessary – as already noted, unless something has gone disastrously wrong, people tend to be resistant to change, particularly if they think they are already doing a perfectly good job. To aid this transition, we always strive to give as much context to the decision-making process as possible.
Establish champions
As such, it is vital that we also establish client champions of the new solution who are already trusted by the fab’s staff, and can help navigate the acceptance process. This is particularly important if, for instance, the decisions that our advanced technology is suggesting initially seem counter-intuitive to those who are familiar and comfortable with old procedures.
Act on feedback
And just as important as demonstrating the results our technology is delivering in a way that’s easy to understand, we also regularly capture user feedback during the rollout period to see where our product and the user experience can be improved. Implementation is a constant process of testing and tweaking to produce the best possible results, and that requires an honest, two-way relationship to be in place. We regularly put new features into our product based on feedback from the shop floor, and it’s always satisfying to hear how we’ve improved operators’ ability to do their jobs as a result.
To undertake a successful smart manufacturing implementation, particularly as a third party vendor, it’s not enough to just have an innovative technology solution. To be a genuine change maker, you need to understand that in the real world, it’s the people that matter as much as the technology. This is why we always set out to build a strong partnership with the fabs that we work with, becoming much more than just an external vendor. Our team is committed to delivering on the KPIs that are targeted by our clients, which doesn’t stop at providing the best possible solution. We also have to understand the people who use it and ensure their adoption of our technology is a smooth and positive process.
Useful resources
Stay up to date with our latest publications.