Scheduling as a Cornerstone of the Smart Factory [Part 1]
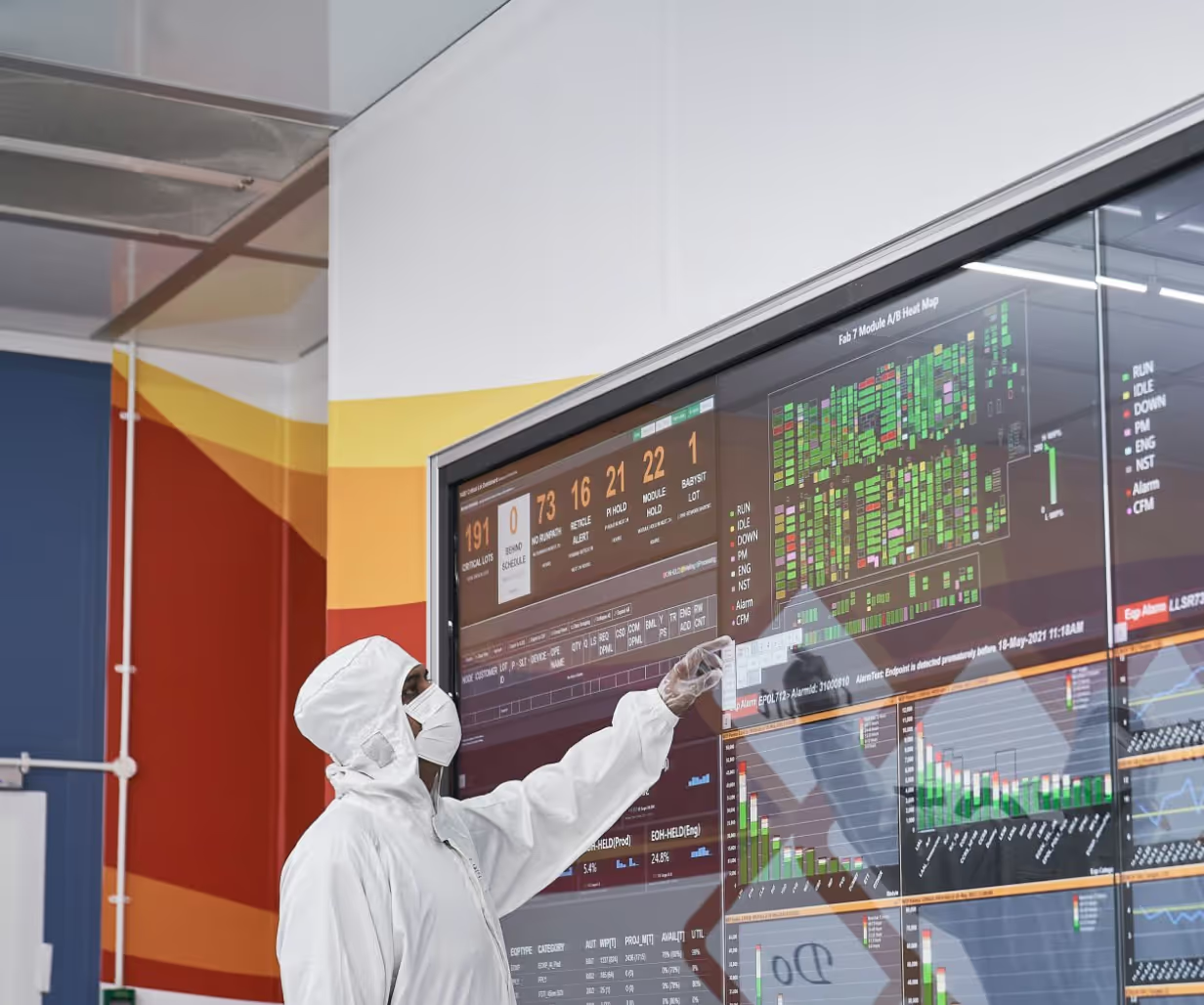
One of the consequences of the pandemic has been an incentive to deglobalise, as regions suffered from the issues with supply chains and geopolitical dependencies. Significant delivery issues in the chip industry – and in particular wafer manufacturing – have had a negative impact on the global economy. However, onshoring this high technology industry will also bring its own challenges. Expertise and cost efficiency to name a couple. Zooming in a bit closer on so-called wafer fabs, we can distinguish two types of factories. The legacy and smaller fabs serving niche markets with older technology nodes, and the cutting-edge giga-factories, recently built or in the making. Both types have different problems to tackle, but one key component of their roadmap could be surprisingly similar.
The newest fabs have well integrated automated systems, but operating them efficiently on such a scale is a challenge of its own. The older factories have the downside of being less automated but they realise the need to become more efficient in energy consumption, labour cost and capacity utilisation. In both situations, digital transformation is coming to the rescue. Industry 4.0 is no longer a buzzword, it has become a matter of regional technological sovereignty.
The fundamental building block of Industry 4.0 is data; an asset which is present in abundance in wafer fabs. So what is preventing these factories from levelling up? The answer is simple, the solution is not: complexity. It’s an inherent part of wafer manufacturing, stemming from; increasingly high numbers of process steps, job shop factory types, re-entrant flows, product diversity, sensitivity to quality issues and so on.
The problem with complex systems is that there’s so much variability and interaction, it's hard to get actionable insights from data. Instead of accepting the stochastic and complex nature of the fab, factories can better control it by using advanced production scheduling to understand in which order lots get processed, on which tool and – the most important difference when compared with common rules-based approaches – when they get processed. To begin, this can be employed in certain bottleneck areas and then once you do it for the entire factory, you get a holistic picture of what is going to happen. Sounds great, doesn’t it? But how exactly will this benefit your fab? To explain, let’s place production scheduling in a couple of recognisable use cases.
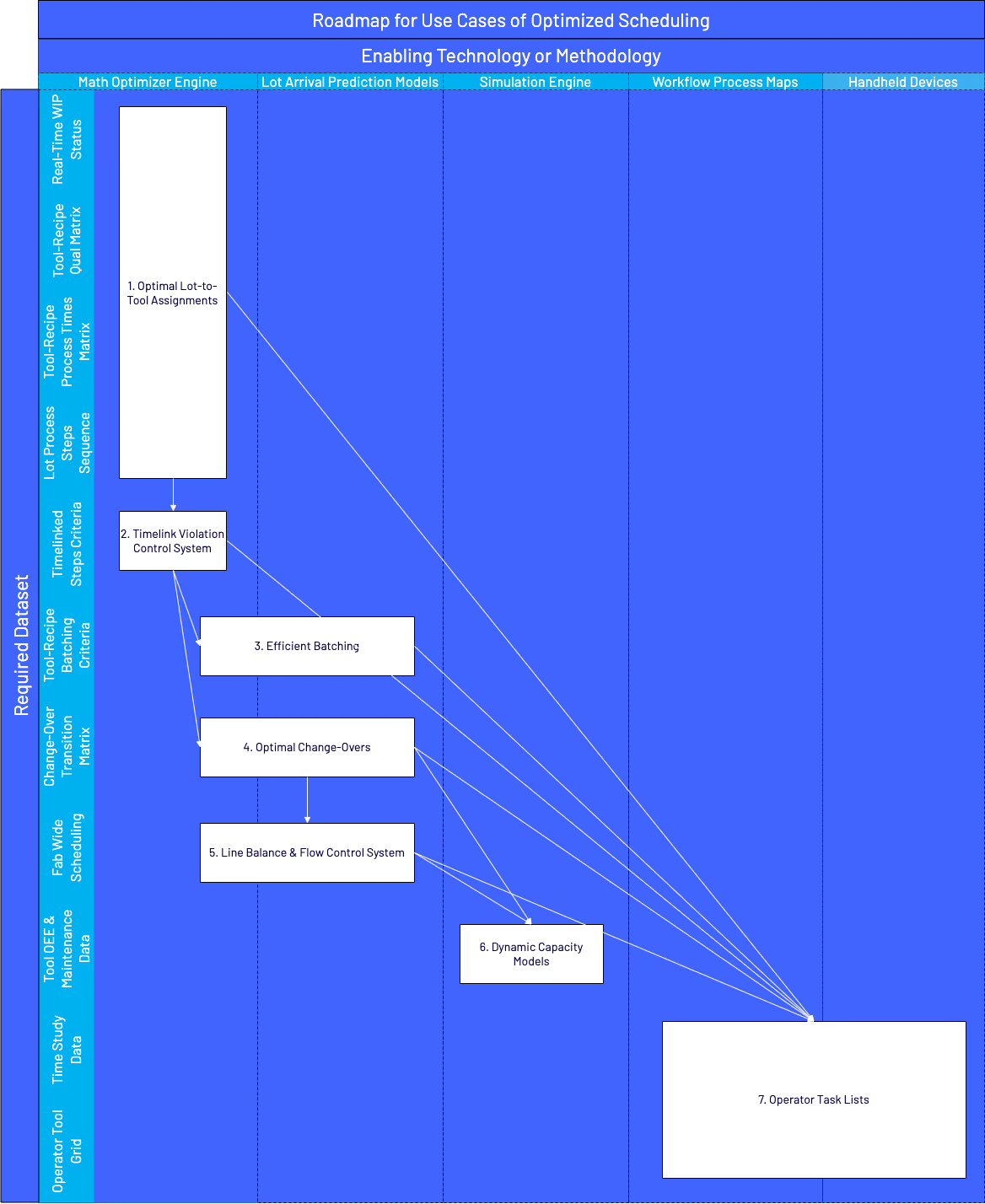
- Lot-Tool Assignments
Wafer manufacturing has complicated recipe-tool qualification matrices within a group of tools that perform similar processes. The weaker tools can process fewer recipes than the stronger ones. We want to avoid stronger tools “stealing” lots away from the weaker tools, because it leaves fewer lots for the weaker tools to process, therefore wasting capacity. The same is true for faster and slower tools: while faster tools are preferred, pushing all the WIP through the faster tools leaves the slower tools under utilised. Advanced schedulers allow for better anticipation of incoming WIP and superior use of available capacity for weak and slow tools. The bigger and more complex the matrix grows, the harder it is to find the optimal processing of WIP. On top of the scheduling itself, mathematical programming helps to optimize lot-to-tool assignments over time. This results in a capacity booster, similar to putting a turbocharger on an engine: it’s the same engine, but with more power.
- Reducing Timelink Violations
Process steps with timelinks are common in wafer manufacturing to control the maximum amount of time a wafer spends between two or more process steps. If a timelink is violated, the wafer requires rework – or worse still, scrappage. A system that avoids timelink violations requires the ability to intelligently plan into the future. And that’s exactly what an advanced scheduler does. It has been proven to drastically reduce timelink violations, even in the most complex of scenarios.
- Improving Batching Efficiency
Batching is a complex decision making process since it involves an estimate of lot arrivals and how waiting longer trades off with running smaller batches. Predicting lot arrivals is difficult in such a complex environment, and trading off wait time against batch efficiency is even harder because the costs and gains are not always clear. Determining and automating this process is well within an advanced scheduler’s remit. Once the algorithm is tuned, it makes the most efficient decision, and perhaps even more importantly: it generates consistent output.
- Optimizing Changeover Decisions
Another use case related to the problem of lot arrivals is the problem of changeover decisions. One toolset with different machine setups can serve multiple different toolsets down the line. A bit like a waiter in a restaurant serving multiple tables. Waiters have to make sure no table is without food or drink, and to do that, they visit the tables regularly to ask for any orders. But for machines, you can’t switch the setup too often because it only increases non-productive time. Preferably, you also plan setup changeovers at a time when planned or predicted downtime for the machine occurs, to reduce downtime variability. To put it simply, it’s a decision on when to switch over from the type A process to the type B process on a tool. An advanced scheduler can solve that equation, finding the optimal point in time. Schedulers are better at this than human reasoning or rule-based logic, as solving to a time dimension is what they are designed for.
- Flow Control and Line Balance
Line balancing is – even for experienced manufacturing engineers – difficult to grasp. One can intuitively understand what it means, but how do you define “balanced” in the first place? Even if you can, it is absolutely beyond the capabilities of a human brain to manually and continuously make decisions that control it. And once it’s out of balance, to recover it. Again, considering the time dimension is a crucial aspect of what advanced schedulers offer, which enables them to recover faster from unforeseen circumstances and maintain better risk-control for generating continuous output.
- Operator Task Lists
As opposed to dispatch lists that only tell the order in which to process lots, advanced schedulers can also tell when a lot is supposed to start and finish processing on a tool. Combine that information with which operators are serving which tools, and you can move away from tool-centric dispatch lists towards operator-centric task lists. With a handheld device, that could even allow you to send push notifications when urgent intervention is needed. It can reduce idle time on tools that have no available operator. Even more so, it can allow for an entire rethink of the workflows operators are used to.
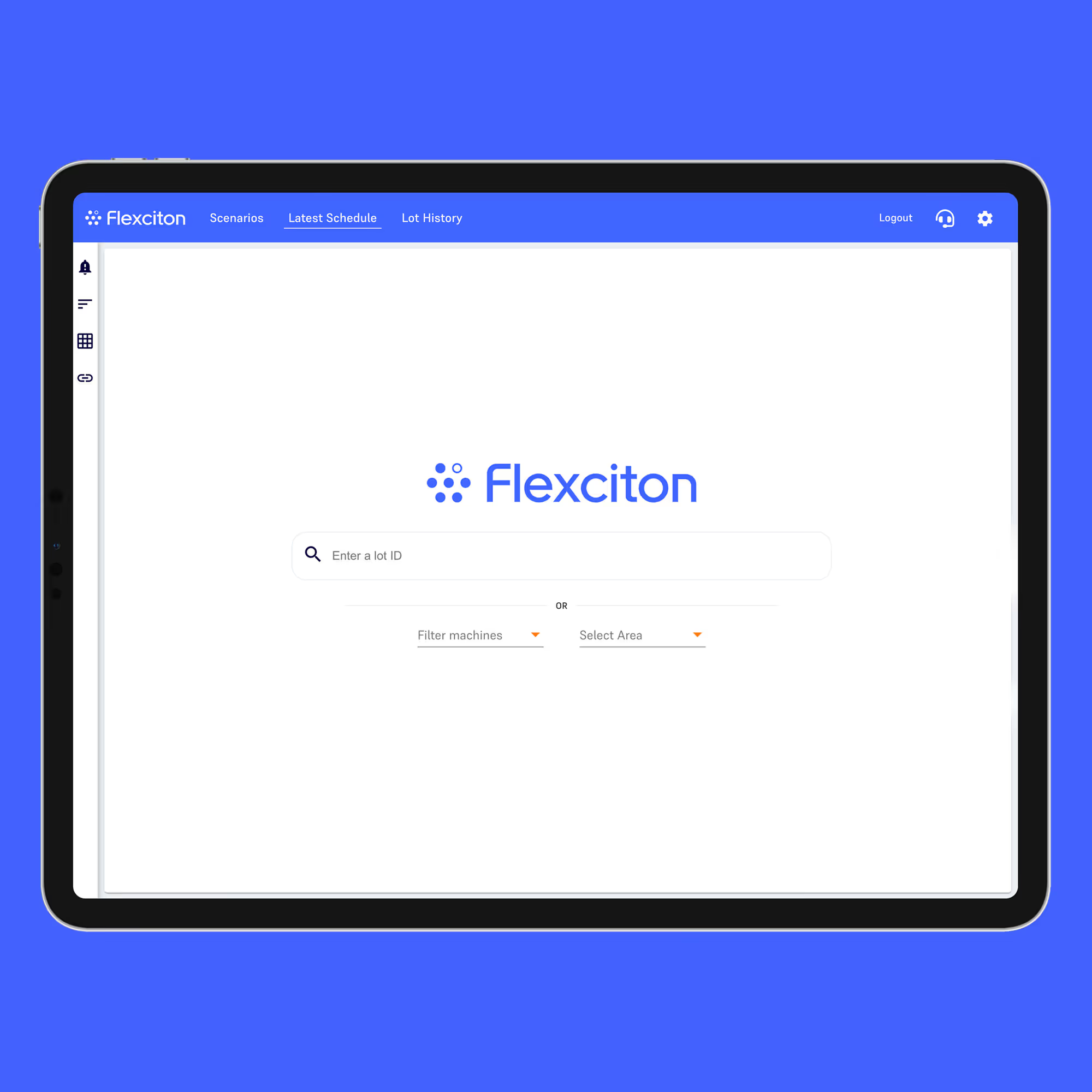
So far in this blog, we’ve focused on scheduling use cases where lots are scheduled on tools, leading to higher throughput on tools, toolsets or the entire factory. All these use cases can also be addressed by improving some rule-based dispatching strategies, but what advanced scheduling offers is the ability to optimize for future decisions rather than just real-time. With that comes better visibility on what will happen in the factory, and it also leaves opportunities for re-organising workflow and freeing up resources. In part 2 of this blog, we’ll begin to look at the future and what could happen when we integrate even further. Enter, Industry 5.0.
Author: Ben Van Damme, Industrial Engineer and Business Consultant
Part 2 is now live. Click to read.
Useful resources
Stay up to date with our latest publications.