It’s Time For The Semiconductor Industry To Embrace Smart Manufacturing
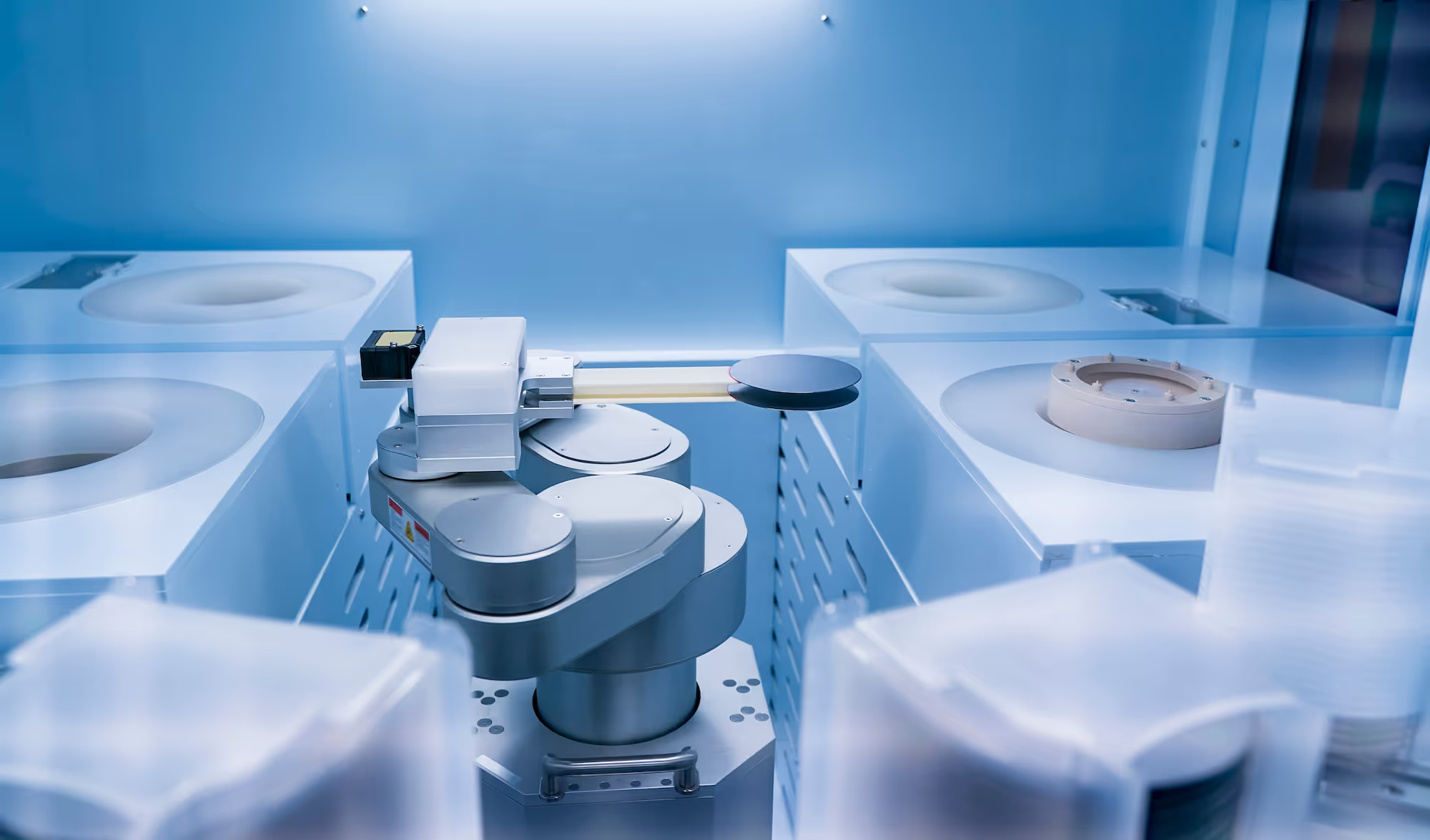
With industries around the world still being hit by semiconductor shortages, chip companies need to embrace smart manufacturing practices to boost production. In this blog, we talk about what those practices are and how to accelerate their adoption.
Long-term capacity issues
The global chip shortage has highlighted that, despite the centrality of silicon to our technology-driven world, the semiconductor industry is far from robust. The Covid-19 pandemic may have created the perfect storm of increased demand versus restricted production. However, this is just the culmination of a long-term struggle to make semiconductor production truly agile which, alongside various geo-political factors, has now exposed the fragility of the semiconductor supply chain for all to see.
The obvious answer to the capacity issue is to build more fabs, but that’s easier said than done. Building a new chip manufacturing facility can take between three to five years, and cost anything from $4bn to $10bn. Undoubtedly more fabs do need to be built, but that isn’t exactly a quick-fix solution when the ongoing chip shortage remains a clear and present danger to industries requiring a constant, uninterrupted supply of semiconductors, from consumer electronics firms to auto manufacturers.
But that’s just to keep us where we are now – what about the R&D and production capacity needed to make the ever more sophisticated, next generation chips required to transition us to a world of ‘smart’, intelligent technologies designed to automate the environment around us and create more sustainable homes and cities? How will we get to this future if we can’t even solve the current bottlenecks that afflict the semiconductor supply chain?
Unsurprisingly, the industry itself has been attempting to address these issues, and look at ways to improve how it works. In the short-term at least, one solution to the capacity problem is to make existing facilities as efficient and productive as possible, and effectively increase capacity without having to build additional fabs.
The smart manufacturing vision
SEMI, the global industry association representing the electronics manufacturing and design supply chain, is attempting to drive this evolution via its Smart Manufacturing initiative. In a nutshell, smart manufacturing is defined as “the use of production and sensor data within manufacturing technologies to enable process adaptability”, ultimately speeding implementation and maximising efficiency. In other words, using the information generated by the factory itself to improve decision making about how best to manufacture products.
SEMI’s vision is to apply smart manufacturing practices across the entire electronic supply chain based on three essential pillars. These are:
- Sensing – establishing the state at any one time of work-in-progress (WIP) and all machines/tools within the fab, including process monitoring and location tracking
- Connecting – ensuring that all this information can be securely transferred to both internal databases and the cloud, for the purposes of creating a ‘digital twin’ of the fab
- Predicting – using the digital twin’s data, via artificial intelligence (AI) and/or machine learning applications, to optimize both WIP scheduling and available resources
SEMI is committed to promote awareness and interest in smart manufacturing practices across the industry, but acknowledges that not every semiconductor company is in the same place. While far from perfect, the industry is reasonably good at capturing data – however, the problem is that this data is often poorly integrated and can effectively become trapped in siloed systems. Without establishing a ‘single version of the truth’ by combining all data sources, it is impossible to create a functioning digital twin with which to improve efficiency.
Acceleration through disruption
To accelerate the rollout of smart manufacturing, we believe that semiconductor companies have to embrace ‘disruptive’ technologies from outside of the industry’s traditional supply chain. It should by now be standard practice for chip companies to actively seek out and adopt best-in-class technology to improve efficiency and boost output. Instead, the decision is often made to develop an in-house alternative. Operating in one of the most technologically cutting-edge industries – with a multitude of engineers and scientists at their disposal – is perhaps one reason why chip manufacturers often look inwards to find solutions to their problems. Searching internally for these complex answers can often mean years spent on researching and millions spent developing, whilst progress already made by academics and disruptive tech companies gets overlooked. The outcome is the same type of systems that have prevented the movement towards SEMI’s third pillar and properly optimizing their fabs’ processes and production.
However, in Flexciton’s experience, this reluctance is easing, with early movers already beginning to enjoy the benefits that come from a fully integrated data environment where AI-based tools can be deployed to improve and automate decision making, and help fabs to work at genuine capacity rather than the ‘false capacity’ that an over-reliance on manual processes and siloed data has created.
For companies to fully embrace smart manufacturing and truly move onto that third pillar, the next step on their journey is to transition away from conventional, heuristic scheduling software that mimics human decision-making process based on historical data. Instead, manufacturers need to adopt advanced technology that makes optimized decisions in real-time with the ability to seamlessly adapt to unpredictable fab environments. By making decisions based on the actual state of the fab and its processes in the present moment, companies can realise even more capacity and see up to 10% extra efficiency in their operations.
The chip shortage may seem like a temporary problem that will soon be resolved – but that’s a dangerous assumption. Instead, it’s a wake-up call that the semiconductor supply chain needs to be re-engineered to become fit for purpose. Fab building may be part of the solution, but more important is the need for existing facilities to be fully optimized in order to realise their true capacity – and that needs the industry to be willing to innovate and pilot cutting edge technologies.
Useful resources
Stay up to date with our latest publications.